SD2 by SIEB & MEYER with Safety Functions SFM and SLOF
Technical papers
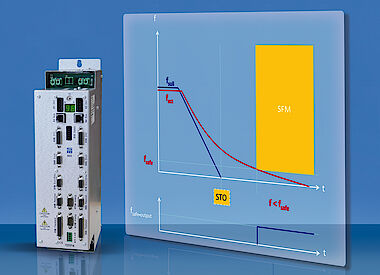
Suited to Sensorless Systems
SIEB & MEYER provides users of the drive amplifiers SD2 with two new safety functions that were especially developed for rotary motors without speed sensors. The solution helps manufacturers of processing machines and machine tools comply with the increasing demands regarding machine efficiency and personal safety.
In the field of processing machines and machine tools, especially with rotating axes, operators and service technicians are exposed to risks due to tools still rotating or rotating at too high speeds. The machine manufacturer faces the challenge of implementing both demands, personal safety and efficiency, optimally as well as in compliance with the relevant standards. The classic safety solutions rely on motors and spindles that are equipped with safe speed sensors to avoid or detect dangerous operating states. Consequently, the machine manufacturer would have to accept lower efficiency of the machines or ensure the required safety integrity level by means of costly safety concepts for each individual application.
Safety Functions for Sensorless Systems
To avoid these compromises SIEB & MEYER has extended the functional spectrum of the well-proven drive amplifier SD2 with the sensorless functions Safe Frequency Monitor (SFM) and Safe Limited Output Frequency (SLOF). Both functions were approved by TÜV Nord according to EN 61508:2010 and meet the requirements of safety integrity level SIL3. In order to implement the new functions the SIEB & MEYER specialists integrated the required hardware and software in the drive amplifiers of series SD2. Both functions are based on the function Safe Torque Off (STO) that is integrated in all SD2 drive amplifiers as standard. The outcome is a cost-effective solution for the machine manufacturer that is suitable for sensorless systems. This makes using spindles and motors without speed sensors possible – a crucial point for applications in the fields of high-speed cutting or grinding, since spindles/motors for these applications are not equipped with speed sensors for technical or financial reasons.
Safe Standstill Monitoring with the Function SFM
By means of the safety function SFM the operator can safely detect whether or not the speed of a sensorless spindle has reached standstill or dropped below a safe speed value after switch-off. As long as this is not the case, a protective door, for example, remains closed. This safety function is used for rotating axes like drilling and routing spindles. The user can parameterize the function SFM, for example, with a limit frequency of 10 Hz. This equals 600 rpm with a 2-pole motor. Up to this speed the risk of injury due to rotating tools is considered low because the user can visually perceive the tool rotation. That means, entering the protected area is determined 'safe'. The function is implemented as sensor signal. Therefore, the function can detect the actual frequency of the motor but cannot limit the rotating field frequency. For this purpose the function SLOF or STO is available
The SFM function is based on a frequency-dependent voltage that is induced by the motor or the remanence. This voltage can be measured at the motor terminals, regardless whether a synchronous motor or an asynchronous motor is used. The drive determines the actual rotating field frequency from that voltage and compares it with the parameterized limit value. If the rotating field frequency is within the parameterized range, the drive generates the status signal "Standstill". The drive amplifier only generates the standstill signal when the output stage is deactivated and the main voltage is switched off. When the output stage is active and/or the main voltage is switched on, the status is always "No Standstill".
Maximum Output Frequency with the Function SLOF
The safety function SLOF is used to make sure that critical speeds are not exceeded. This can protect persons and equipment, for example, when a tool might break due to overspeed. For this purpose the function determines the actual rotating field frequency and compares it with the parameterized limit value. If the rotating field frequency is within the parameterized range, the drive generates the status signal "Frequency In Limits". If the limit value is exceeded, the output stage is disabled via the function STO. The system stops generating torque and thus acceleration at once. In this case the function status is "Frequency Out Of Limits"
Hence, the function SLOF allows defining a safe limit for the rotating field of a spindle. This prevents that the drive actively accelerates the connected spindle to a too high frequency. When an external system actively accelerates the spindle, though, the function cannot prevent exceeding the limit frequency. If the set maximum rotating field frequency is exceeded because of a faulty input or malfunction of the drive amplifier, the function STO disables the output stage.
Customized Solutions Available
Manufacturers of processing machines and machine tools benefit greatly from the two new safety functions for SD2. In addition, the solution fills a gap in the market – in line with the motto of SIEB & MEYER regarding the continuous development of well-proven products based on customer needs. By the way, the Lueneburg based company develops special demands as customized solutions: On the basis of the existing device platforms SD2x and SD4x SIEB & MEYER implements solutions for high-speed applications with synchronous and asynchronous motors up to 8,000 Hz (480,000 rpm) as well as dynamic motion applications, e.g. in the press and tightening industry. Initially, the customer defines the required functions for the hardware and the software of the device. This ensures optimal adapting of construction, dimensions and interfaces as well as electric performance dimensioning to the specific conditions of the application.