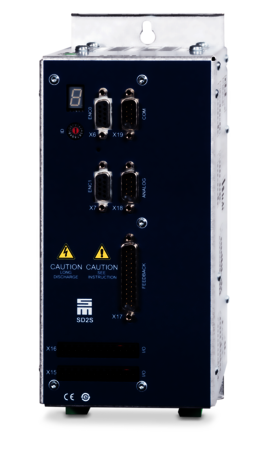
Servo Drive SD2S
Powerful, flexible, low cost – these words describe the servo drive SD2S by SIEB & MEYER. The compact dimensions allow space-saving design of the switch cabinet. Linear motors, rotary servo motors, high-pole torque motors as well as synchronous/asynchronous tool spindles with or without sensor can be driven by SD2S.
For the connection to a higher-ranking control analog reference values (+/-10 V) or pulse-direction values, CAN bus or PROFIBUS* signals and protocols are processed. Alternatively, a CNC control can be connected via the bus system SERVOLINK 4. The communication via EtherCAT (CoE)** is optinally provided
* Via gateway
** CoE = CAN over EtherCAT
Highlights
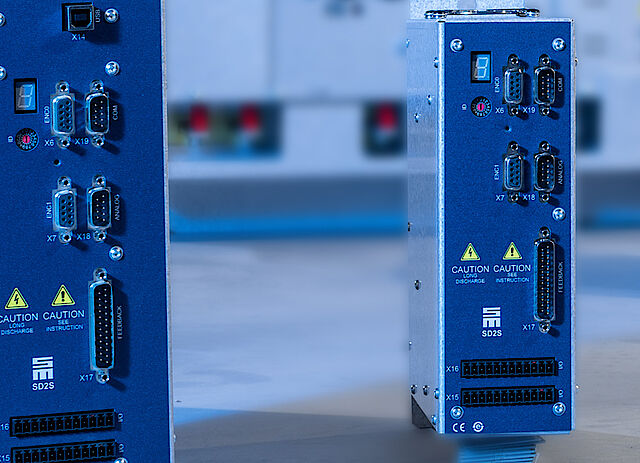
The Smart Drive for Servo Applications
Universal Motor Encoder Interface
SD2S evaluates all common measuring systems for rotary and linear motors. The drive controls systems with absolute value encoders with EnDat, Hiperface or SSI interface, encoders, magnetoresistive sensors, Hall effect sensors, linear Hall sensors, linear scales with 1Vpp or TTL level as well as resolvers.
Safety Integrated
The currently effective safety category 4 can be reached by the integrated restart lock. As external protective circuits can be reduced, system costs are minimized.
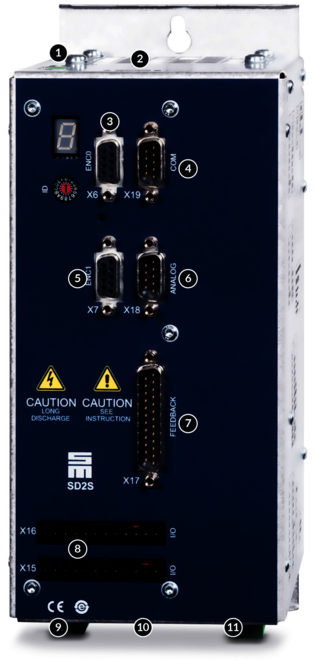
The Interfaces of Servo Drive SD2S
- Safety integrated "STO":
Restart lock to meet category 4/PL e according to EN ISO 13849-1:2015 and EN 61508:2010 SIL3 - USB connection, parameterization, diagnosis and operation
- 2 TTL encoder inputs and outputs
- RS232 / CAN interface
- 2 TTL encoder inputs and outputs
- 2 analog reference value interfaces: +/-10 V;
2 analog outputs: 0-10 V - Universal motor encoder interface:
Hall sensor, linear Hall sensor, magnetoresistive sensor, NAMUR Sensor (pulse generator), Sin/Cos encoder, resolver - 9 digital inputs and 5 digital outputs
- SERVOLINK 4 via optical fiber PROFIBUS adapter
- Power supply
- Motor connection
PROFIBUS and PROFINET via gateway
Optional: EtherCAT (CoE)
Drive Functions and Safety Functions
Software for Initial Operation and Parameterization: drivemaster2
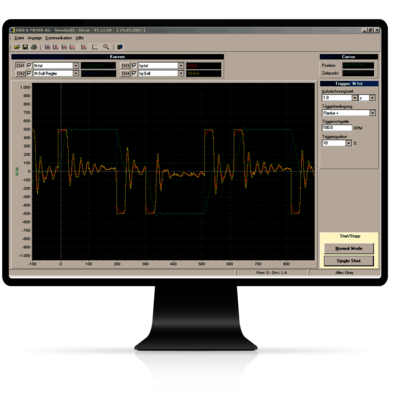
The oscilloscope function allows optimization of the axes in the machine via the drive-setup-tool without additional measuring equipment.
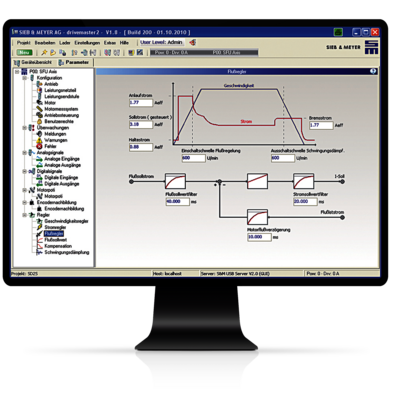
The clear design of the software allows intuitive parameterization via graphics and block diagrams. The „Parameter-Wizard“ guides the user step-by-step through the system configuration and allows intuitive setup of the device via help messages and comments.
Technical Specifications of Servo Drive SD2S
Device type | Rated power1 | Rated current | Peak current/time | Max. output voltage1 | HxWxD (mm) | Weight | Cooling |
---|---|---|---|---|---|---|---|
Compact devices - 1 x 50 VAC power supply | |||||||
0362X40DA | 330 VA | 10 Arms | 14 Arms/5 s | 3 x 45 VAC | 249 x 70 x 188 | 2.5 kg | Air |
Compact devices - 1 x 110...230 VAC power supply | |||||||
0362X40DC | 1.5 kVA | 10 Arms | 14 Arms/5 s | 3 x 200 VAC | 249 x 70 x 188 | 2.5 kg | Air |
0362X40EC | 1.5 kVA | 10 Arms | 28 Arms/2 s | 3 x 200 VAC | 249 x 70 x 188 | 2.5 kg | Air |
Compact devices - (3)1 x 110...230 VAC power supply | |||||||
0362X41EC | 3.8 kVA (6.9 kVA2) | 20 Arms | 28 Arms/5 s | 3 x 200 VAC | 253 x 104 x 188 | 3.5 kg | Air |
0362X41IC | 3.8 kVA (6.9 kVA2) | 20 Arms | 56 Arms/2 s | 3 x 200 VAC | 253 x 104 x 188 | 3.5 kg | Air |
Compact devices - 3 x 200...480 VAC power supply | |||||||
0362X40EF | 4.3 kVA | 7 Arms | 28 Arms5 s | 3 x 410 VAC | 249 x 70 x 232 | 3.5 kg | Air |
0362X41EF | 9.7 kVA | 14 Arms | 28 Arms/5 s | 3 x 410 VAC | 253 x 104 x 188 | 3.5 kg | Air |
0362X41IF | 9.7 kVA | 14 Arms | 56 Arms/2 s | 3 x 410 VAC | 253 x 104 x 188 | 3.5 kg | Air |
0362X49IF3) | 9.7 kVA | 14 Arms | 56 Arms/0,4 s | 3 x 410 VAC | 279 x 90 x 220 | 3.9 kg | Air |
0362X45EF | 15.9 kVA | 23 Arms | 28,3 Arms/5 s | 3 x 410 VAC | 390 x 181 x 178 | 7.8 kg | Air |
0362X45IF | 20.8 kVA | 30 Arms | 56,6 Arms/2 s | 3 x 410 VAC | 390 x 181 x 178 | 7.8 kg | Air |
0362X46IF | 24.2 kVA | 35 Arms | 56,6 Arms/5 s | 3 x 410 VAC | 460 x 190 x 220 | 13.7 kg | Air |
0362X46LF | 30.5 kVA | 44 Arms | 70,7 Arms/5 s | 3 x 410 VAC | 460 x 190 x 220 | 13.7 kg | Air |
0362X48MF | 55.4 kVA | 80 Arms | 113 Arms/5 s | 3 x 410 VAC | 429 x 272 x 265 | 19 kg | Air |
0362X48OF | 55.4 kVA | 80 Arms | 113 Arms/5 s | 3 x 410 VAC | 429 x 200 x 262 | 15 kg | Water |
X = 1: CAN bus
X = 2: EtherCAT and CAN bus
1) Rated power and max. output voltage for mains voltage/supply voltage (in italic)
2) Output power for three-phase mains
3) NRTL certified
News
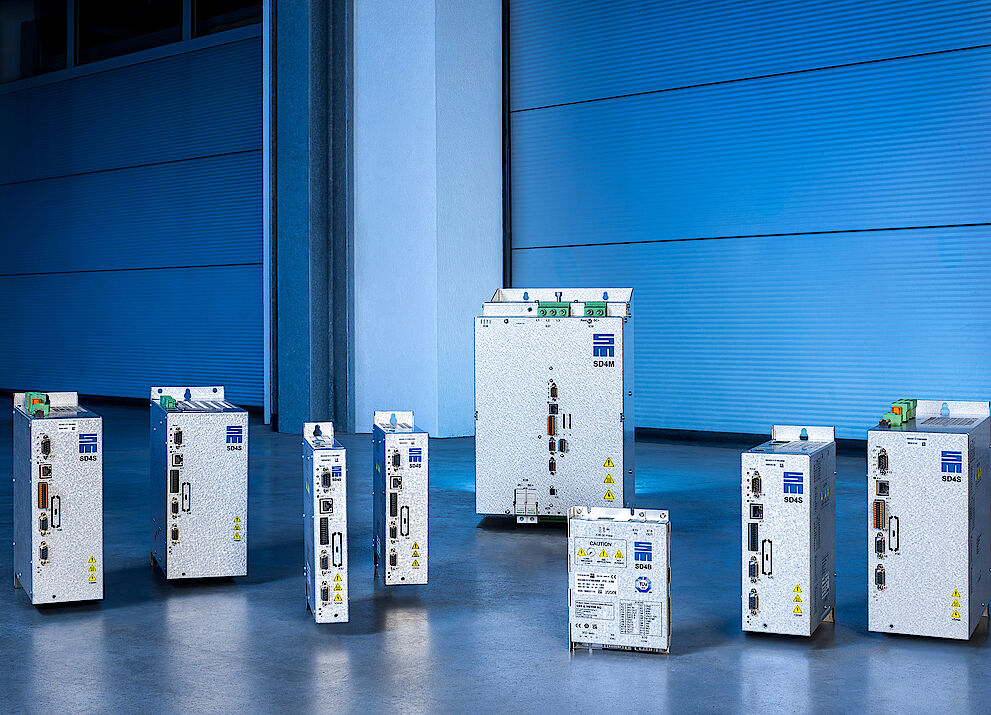
A Drive Controller for All Purposes
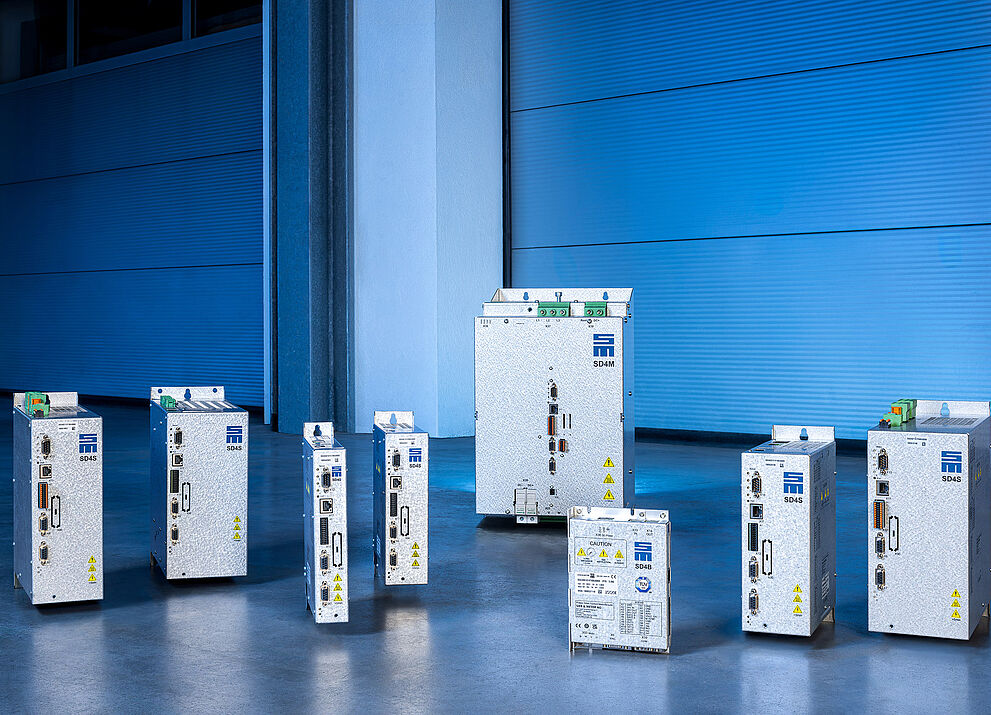
The Best of Two Worlds
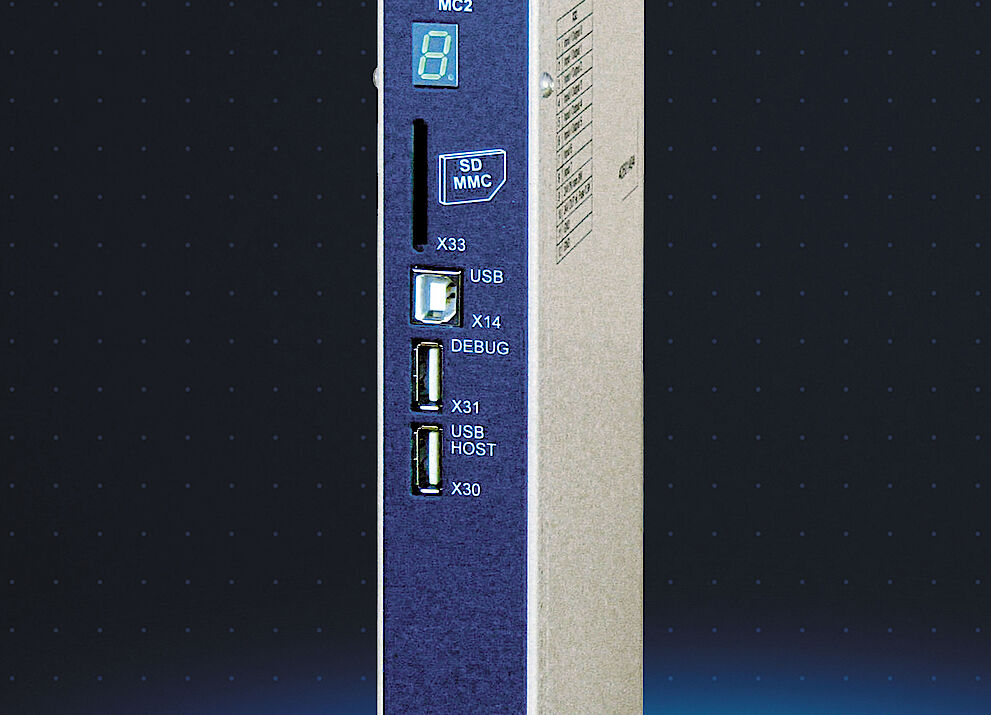
Highly Precise Movement of up to 8 Axes
Feel free to contact us
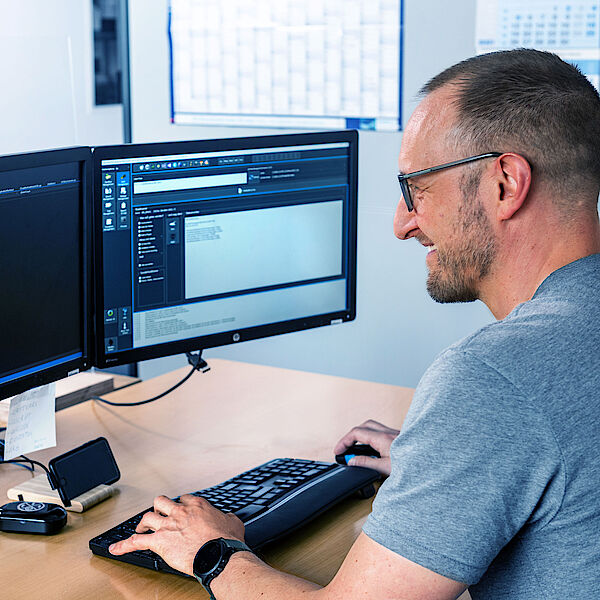
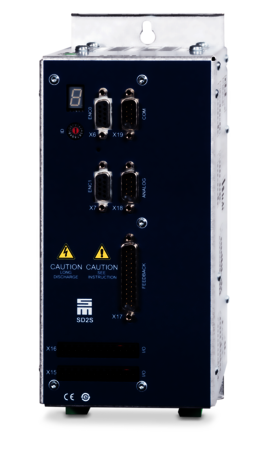
Servo Drive SD2S
Powerful, flexible, low cost – these words describe the servo drive SD2S by SIEB & MEYER. The compact dimensions allow space-saving design of the switch cabinet. Linear motors, rotary servo motors, high-pole torque motors as well as synchronous/asynchronous tool spindles with or without sensor can be driven by SD2S.
For the connection to a higher-ranking control analog reference values (+/-10 V) or pulse-direction values, CAN bus or PROFIBUS* signals and protocols are processed. Alternatively, a CNC control can be connected via the bus system SERVOLINK 4. The communication via EtherCAT (CoE)** is optinally provided
* Via gateway
** CoE = CAN over EtherCAT
Highlights
Small Construction Volume
- Function: Provides a high nominal/peak current ratio.
- Advantage: Use of a smaller device in applications with short overload requirements.
- Benefit: Lower costs and construction volume.
Universal Motor Encoder Interface
- Function: Resolver, encoder / linear scale (TTL or Sin/Cos), EnDat, Hiperface, SSI, Hall sensor, linear Hall sensor, magnetoresistive sensor, NAMUR sensor.
- Advantage: High flexibility in the choice of the motor encoder interface.
- Benefit: Low system costs, free choice of the motor manufacturer.
Safety Integrated
- Function: Safety function STO integrated as standard.
- Advantage: No external components such as power contactors.
- Benefit: Reduction of the system costs.
The Smart Drive for Servo Applications
Universal Motor Encoder Interface
SD2S evaluates all common measuring systems for rotary and linear motors. The drive controls systems with absolute value encoders with EnDat, Hiperface or SSI interface, encoders, magnetoresistive sensors, Hall effect sensors, linear Hall sensors, linear scales with 1Vpp or TTL level as well as resolvers.
Safety Integrated
The currently effective safety category 4 can be reached by the integrated restart lock. As external protective circuits can be reduced, system costs are minimized.
The Interfaces of Servo Drive SD2S
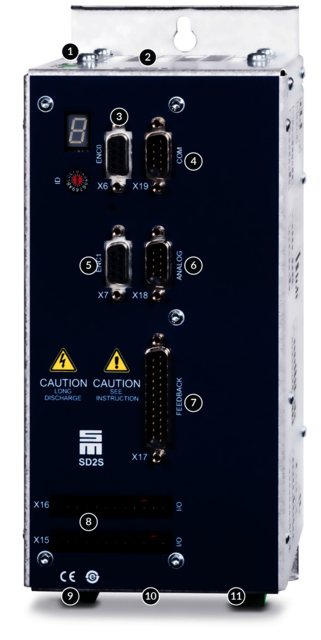
- Safety integrated "STO":
Restart lock to meet category 4/PL e according to EN ISO 13849-1:2015 and EN 61508:2010 SIL3 - USB connection, parameterization, diagnosis and operation
- 2 TTL encoder inputs and outputs
- RS232 / CAN interface
- 2 TTL encoder inputs and outputs
- 2 analog reference value interfaces: +/-10 V;
2 analog outputs: 0-10 V - Universal motor encoder interface:
Hall sensor, linear Hall sensor, magnetoresistive sensor, NAMUR Sensor (pulse generator), Sin/Cos encoder, resolver - 9 digital inputs and 5 digital outputs
- SERVOLINK 4 via optical fiber PROFIBUS adapter
- Power supply
- Motor connection
PROFIBUS and PROFINET via gateway
Optional: EtherCAT (CoE)
Drive Functions and Safety Functions
Software for Initial Operation and Parameterization: drivemaster2
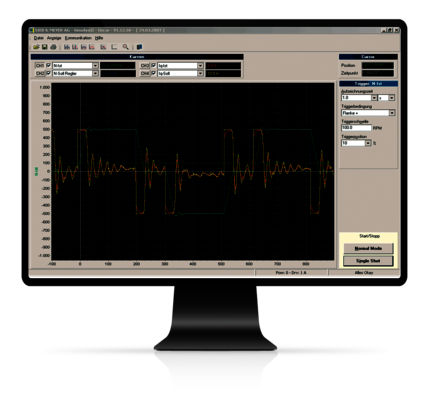
The oscilloscope function allows optimization of the axes in the machine via the drive-setup-tool without additional measuring equipment.
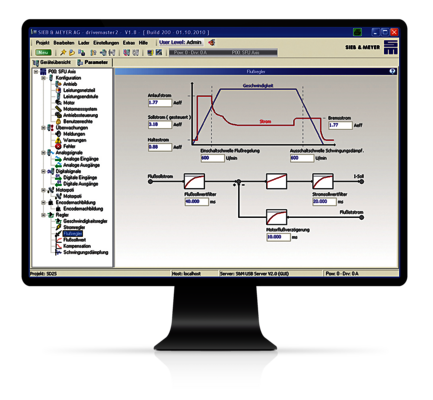
The clear design of the software allows intuitive parameterization via graphics and block diagrams. The „Parameter-Wizard“ guides the user step-by-step through the system configuration and allows intuitive setup of the device via help messages and comments.
Technical Specifications of Servo Amplifier SD2S
Device type | Rated power1 | Rated current | Peak current/time | Max. output voltage1 | HxWxD (mm) | Weight | Cooling |
---|---|---|---|---|---|---|---|
Compact devices - 1 x 50 VAC power supply | |||||||
0362X40DA | 330 VA | 10 Arms | 14 Arms/5 s | 3 x 45 VAC | 249 x 70 x 188 | 2.5 kg | Air |
Compact devices - 1 x 110...230 VAC power supply | |||||||
0362X40DC | 1.5 kVA | 10 Arms | 14 Arms/5 s | 3 x 200 VAC | 249 x 70 x 188 | 2.5 kg | Air |
0362X40EC | 1.5 kVA | 10 Arms | 28 Arms/2 s | 3 x 200 VAC | 249 x 70 x 188 | 2.5 kg | Air |
Compact devices - (3)1 x 110...230 VAC power supply | |||||||
0362X41EC | 3.8 kVA (6.9 kVA2) | 20 Arms | 28 Arms/5 s | 3 x 200 VAC | 253 x 104 x 188 | 3.5 kg | Air |
0362X41IC | 3.8 kVA (6.9 kVA2) | 20 Arms | 56 Arms/2 s | 3 x 200 VAC | 253 x 104 x 188 | 3.5 kg | Air |
Compact devices - 3 x 200...480 VAC power supply | |||||||
0362X40EF | 4.3 kVA | 7 Arms | 28 Arms5 s | 3 x 410 VAC | 249 x 70 x 232 | 3.5 kg | Air |
0362X41EF | 9.7 kVA | 14 Arms | 28 Arms/5 s | 3 x 410 VAC | 253 x 104 x 188 | 3.5 kg | Air |
0362X41IF | 9.7 kVA | 14 Arms | 56 Arms/2 s | 3 x 410 VAC | 253 x 104 x 188 | 3.5 kg | Air |
0362X49IF3) | 9.7 kVA | 14 Arms | 56 Arms/0,4 s | 3 x 410 VAC | 279 x 90 x 220 | 3.9 kg | Air |
0362X45EF | 15.9 kVA | 23 Arms | 28,3 Arms/5 s | 3 x 410 VAC | 390 x 181 x 178 | 7.8 kg | Air |
0362X45IF | 20.8 kVA | 30 Arms | 56,6 Arms/2 s | 3 x 410 VAC | 390 x 181 x 178 | 7.8 kg | Air |
0362X46IF | 24.2 kVA | 35 Arms | 56,6 Arms/5 s | 3 x 410 VAC | 460 x 190 x 220 | 13.7 kg | Air |
0362X46LF | 30.5 kVA | 44 Arms | 70,7 Arms/5 s | 3 x 410 VAC | 460 x 190 x 220 | 13.7 kg | Air |
0362X48MF | 55.4 kVA | 80 Arms | 113 Arms/5 s | 3 x 410 VAC | 429 x 272 x 265 | 19 kg | Air |
0362X48OF | 55.4 kVA | 80 Arms | 113 Arms/5 s | 3 x 410 VAC | 429 x 200 x 262 | 15 kg | Water |
X = 1: CAN bus
X = 2: EtherCAT and CAN bus
1) Rated power and max. output voltage for mains voltage/supply voltage (in italic)
2) Output power for three-phase mains
3) NRTL certified
Applications
About SIEB & MEYER
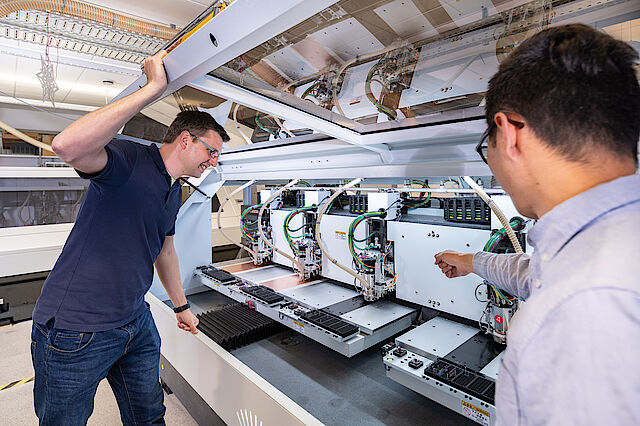
SIEB & MEYER AG - Drive and control solutions of the latest generation
SIEB & MEYER was founded in 1962 and is a successful company in the field of industrial electronics. With around 260 employees worldwide today, we develop and manufacture control technology and drive electronics. Our core technologies include controllers for mechanical engineering and automation technology, servo amplifiers for a wide range of drives and frequency converters for high-speed motors and generators.
Contact
SIEB & MEYER AG
Auf dem Schmaarkamp 21
D-21339 Lüneburg
Phone: +49 4131 203 0
Fax: +49 4131-203 2000
You can find all sales contacts at: www.sieb-meyer.com/contact/sales
You can find all agencies and partners at: www.sieb-meyer.com/contact/offices-and-sales-partners