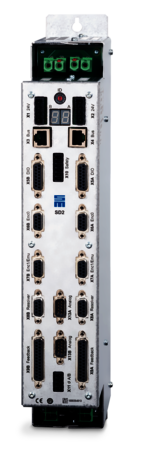
Drive Controller SD2
The drive controller SD2 is designed to control synchronous and asynchronous motors with or without a sensor and permits quick and easy adaptation to the individual case of application – whether used with linear motors, rotary motors or motor-driven machining spindles.
This universal drive solution allows realization of high-speed applications up to 360,000 rpm (6,000 Hz). Universal motor encoder interfaces and different connection possibilities to a higher-ranking control allow easy adaptation to changing system requirements – nothing will stand in the way of the optimal realization of multi-axis applications.
Highlights
The Team Player
As a standard all devices of series SD2 are equipped with "Safe Torque Off" (STO). The sensorless safety functions "Safe Frequency Monitor" (SFM) and "Safe Limited Output Frequency” (SLOF) are available as option.
This is a great benefit to allow compliance with the requirements of the Machinery Directive.
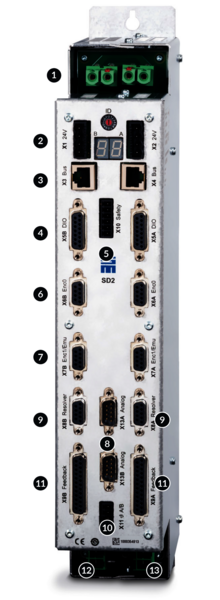
The Interfaces of SD2 (Two-channel Device)
- Mains supply (DC)
- 24 V-Logic supply
- Parameterization and diagnosis
- 6 digital inputs and 4 digital outputs
- Safety integrated "STO": Restart lock to meet category 4/PL e according to EN ISO 13849-1:2015 and EN 61508:2010 SIL3
- Encoder inputs and outputs (Puls-direction signals)
- Encoder inputs and outputs (measuring system simulation)
- Analog reference value interfaces: +/-10 V
- Resolver inputs
- Thermal contacts
- Universal motor encoder interface: Encoder / linear scale(TTL or Sin/Cos), EnDat, Hiperface, SSI, Hall effect sensor, linearer Hall sensor, magnetoresistive sensor
- SERVOLINK 4 via optical fiber connector
- 2 x Motor connection for synchronous / asynchronous spindles, linear motors and rotary motors
EtherCAT, PROFIBUS and PROFINET via gateway
Drive Functions and Safety Functions
Software for Initial Operation and Parameterization: drivemaster2
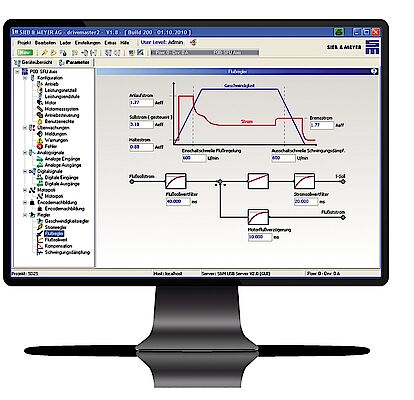
Parameterization
- Tree-type structure
- Block diagrams
- Graphics
- Interactive help messages
- Comments
- „Parameter-Wizard“
- Saving and reloading of projects, parameter files and motor parameters
- Centralized access to all axes
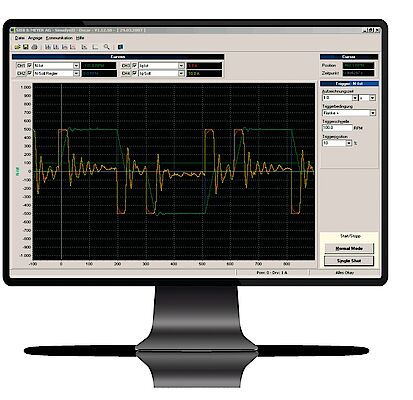
Diagnosis
- 4-channel oscilloscope
- Zoom functions
- Trigger functions
- Long-term recording function
- Measurements can be saved
- Diagnosis of the inputs and outputs
- Bus monitor
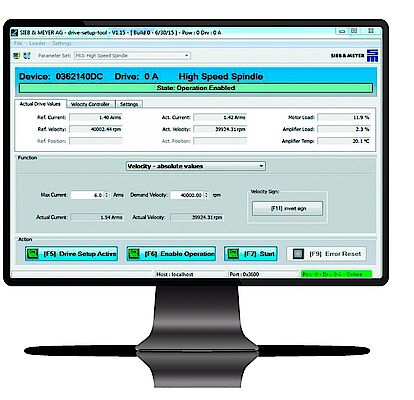
Operation
- Without higher-ranking control
- Visualized reference and actual values
- Error and status messages
Technical Specifications SD2 with Integrated Heat Sink
Device type | Rated power1 | Rated current | Peak current/time | Max. output voltage1 | HxWxD (mm) | Weight | Cooling |
---|---|---|---|---|---|---|---|
Single drive controller - 325 VDC supply voltage | |||||||
0362114IC | 8.6 kVA | 25 Arms | 56.6 Arms/2 s | 3 x 200 VAC | 410 x 70 x 207 | 5.7 kg | Air |
Single drive controller - 560...680 VDC supply voltage | |||||||
0362114EF | 9.9 kVA | 14 Arms | 28.3 Arms/2 s | 3 x 410 VAC | 410 x 70 x 207 | 5.7 kg | Air |
0362114IF | 9.9 kVA | 14 Arms | 56.6 Arms/2 s | 3 x 410 VAC | 410 x 70 x 207 | 5.7 kg | Air |
0362114MF | 24.8 kVA | 35 Arms | 113 Arms/2 s | 3 x 410 VAC | 410 x 130 x 207 | 9.3 kg | Air |
0362114NF | 24.8 kVA | 35 Arms | 141 Arms/2 s | 3 x 410 VAC | 410 x 130 x 207 | 9.3 kg | Air |
0362111RF | 78 kVA | 127 Arms | 177 Arms/25 s | 3 x 410 VAC | 390 x 230 x 144 | 8.7 kg | Water |
0362111SF | 141 kVA | 200 Arms | 245 Arms/25 s | 3 x 410 VAC | 410 x 230 x 180 | 11 kg | Water |
Double drive controller - 325 VDC supply voltage | |||||||
0362113EEC | 3.5 kVA + 3.5 kVA | 10 Arms + 10 Arms | 28.3 Arms/2 s + 28.3 Arms/2 s | 3 x 200 VAC | 410 x 70 x 207 | 5.7 kg | Air |
Double drive controller - 560...680 VDC supply voltage | |||||||
0362113CCF | 4.5 kVA + 4.5 kVA | 6,4 Arms + 6,4 Arms | 7,1 Arms/5 s + 7,1 Arms/5 s | 3 x 410 VAC | 249 x 70 x 232 | 5.7 kg | Air |
0362113EEF | 5 kVA + 5 kVA | 7 Arms + 7 Arms | 28,3 Arms/2 s + 28,3 Arms/2 s | 3 x 410 VAC | 249 x 70 x 232 | 5.7 kg | Air |
Double compact devices - (1)3 x 110...230 VDC mains voltage | |||||||
0362131DDC | 6.4 kVA | 11 Arms + 11 Arms | 14 Arms/5 s + 14 Arms/5 s | 3 x 200 VAC | 410 x 100 x 207 | 7.5 kg | Air |
0362131SSC | 6.4 kVA | 11 Arms + 11 Arms | 42 Arms/1 s + 42 Arms/1 s | 3 x 200 VAC | 410 x 100 x 207 | 7.5 kg | Air |
1) Rated power and max. output voltage for mains voltage/supply voltage (in italic)
SD2 with Integrated Heat Sink
Device type | Rated power1 | Rated current | Peak current/time | Max. output voltage1 | HxWxD (mm) | Weight | Cooling |
---|---|---|---|---|---|---|---|
Double compact devices - 3 x 400...480 VDC mains voltage | |||||||
362131DDF | 11.2 kVA | 7 Arms+ 7 Arms | 42 Arms/1 s + 42 Arms/1 s | 3 x 410 VAC | 410 x 100 x 207 | 7.5 kg | Air |
Technical Specifications of PS2 Power Supply Unit with Integrated Heat Sink
Device type | Rated power1 | HxWxD (mm) | Weight | Cooling |
---|---|---|---|---|
Power supply unit - 3 x 110...480 VAC mains voltage | ||||
0362191F | 27 kW | 410 x 70 x 207 | 5.8 kg | Air |
0362193F | 72 kW | 410 x 160 x 207 | 9.35 kg | Air |
1) Rated power and max. output voltage for mains voltage/supply voltage (in italic)
Technical Specifications of SD2 with Integrated Heat Sink and Safety Functions SFM/SLOF
Device type | Rated power1 | Rated current | Peak current/time | Max. output voltage1 | HxWxD (mm) | Weight | Cooling |
---|---|---|---|---|---|---|---|
Single drive controller - 560...680 VDC supply voltage | |||||||
0362314DF | 8 kVA | 11.3 Arms | 14.1 Arms/5 s | 3 x 410 VAC | 410 x 70 x 209 | 5.7 kg | Air |
0362414EF | 14.2 kVA | 20 Arms | 28.3 Arms/2 s | 3 x 410 VAC | 410 x 70 x 209 | 5.7 kg | Air |
0362414QF | 30 kVA | 42 Arms | 85 Arms/2 s | 3 x 410 VAC | 415 x 135 x 218 | 7.0 kg | Air |
0362414RF | 85 kVA | 120 Arms | 177 Arms/15 s | 3 x 410 VAC | 410 x 103 x 209 | 6.5 kg | Air |
Double drive controller - 560...680 VDC supply voltage | |||||||
0362413DDF | 6.4 kVA + 6.4 kVA | 9 Arms + 9 Arms | 14 Arms/5 s + 14 Arms/5 s | 3 x 410 VAC | 410 x 70 x 207 | 5.7 kg | Air |
1) Rated power and max. output voltage for mains voltage/supply voltage (in italic)
2) Output power at three-phase mains
SD2 for Cold-plate Mounting
Device type | Rated power1 | Rated current | Peak current/time | Max. output voltage1 | HxWxD (mm) | Weight | Cooling |
---|---|---|---|---|---|---|---|
Single drive controller - 680 VDC supply voltage | |||||||
0362111EF | 7.8 kVA | 11 Arms | 28 Arms/2 s | 3 x 410 VAC | 410 x 70 x 134 | 3 kg | Cold-Plate |
0362111IF | 11.4 kVA | 16 Arms | 56 Arms/1 s | 3 x 410 VAC | 410 x 70 x 134 | 3 kg | Cold-Plate |
0362111NF | 24.8 kVA | 35 v | 141 Arms/2 s | 3 x 410 VAC | 410 x 130 x 134 | 9 kg | Cold-Plate |
Double drive controller - 680 VDC supply voltage | |||||||
0362110DDF | 7.8 kVA + 7.8 kVA | 11 Arms + 11 Arms | 14 Arms/5 s + 14 Arms/5 s | 3 x 410 VAC | 410 x 70 x 134 | 3 kg | Cold-Plate |
0362110EEF | 7.8 kVA + 7.8 kVA | 11 Arms + 11 Arms | 28 Arms/5 s + 28 Arms/5 s | 3 x 410 VAC | 410 x 70 x 134 | 3 kg | Cold-Plate |
Double compact devices - (1)3 x 110...230 VDC mains voltage | |||||||
0362130SSC | 6.4 kVA | 11 Arms + 11 Arms | 42 Arms/1 s + 42 Arms/1 s | 3 x 200 VAC | 410 x 100 x 207 | 7.5 kg | Cold-Plate |
Double compact devices - 3 x 400...480 VDC mains voltage | |||||||
0362130DDF | 11.2 kVA | 7 Arms + 7 Arms | 14 Arms/5 s + 14 Arms/5 s | 3 x 410 VAC | 410 x 100 x 207 | 7.5 kg | Cold-Plate |
0362130SSF | 11.2 kVA | 7 Arms + 7 Arms | 42 Arms/1 s + 42 Arms/1 s | 3 x 410 VAC | 410 x 100 x 207 | 7.5 kg | Cold-Plate |
1) Rated power and max. output voltage for mains voltage/supply voltage (in italic)
News
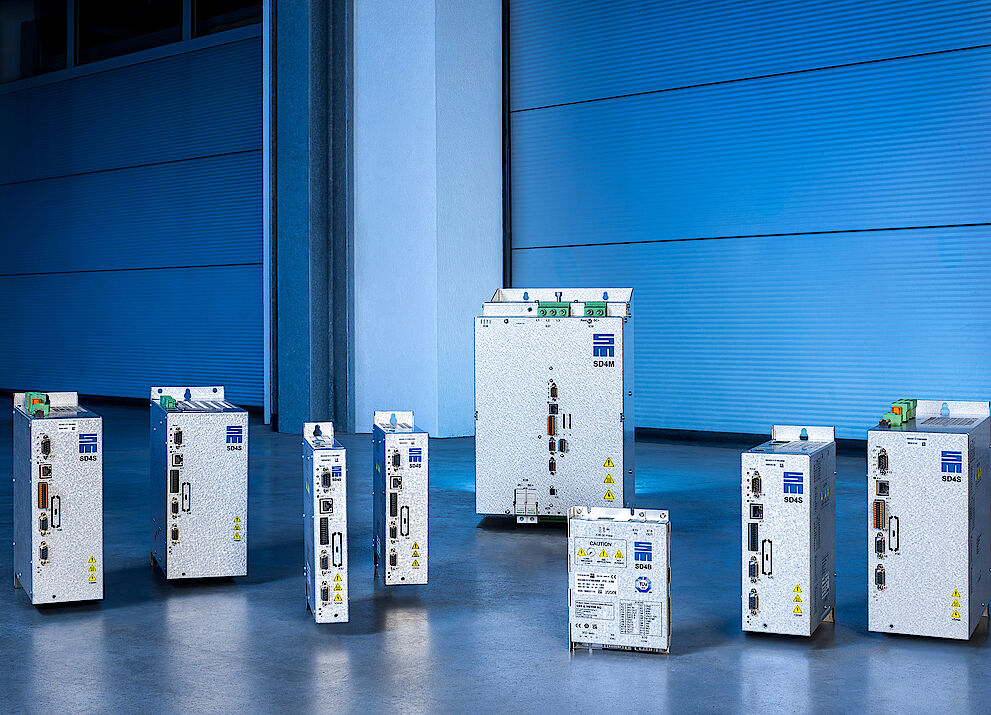
A Drive Controller for All Purposes
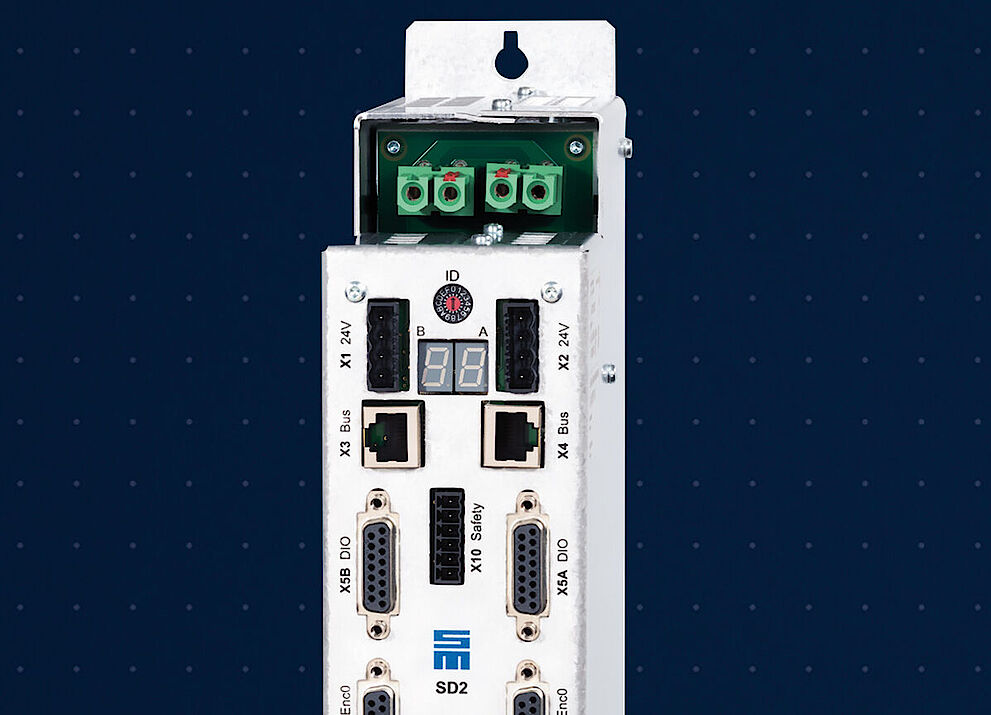
More Efficiency at Lower CO₂ Emissions
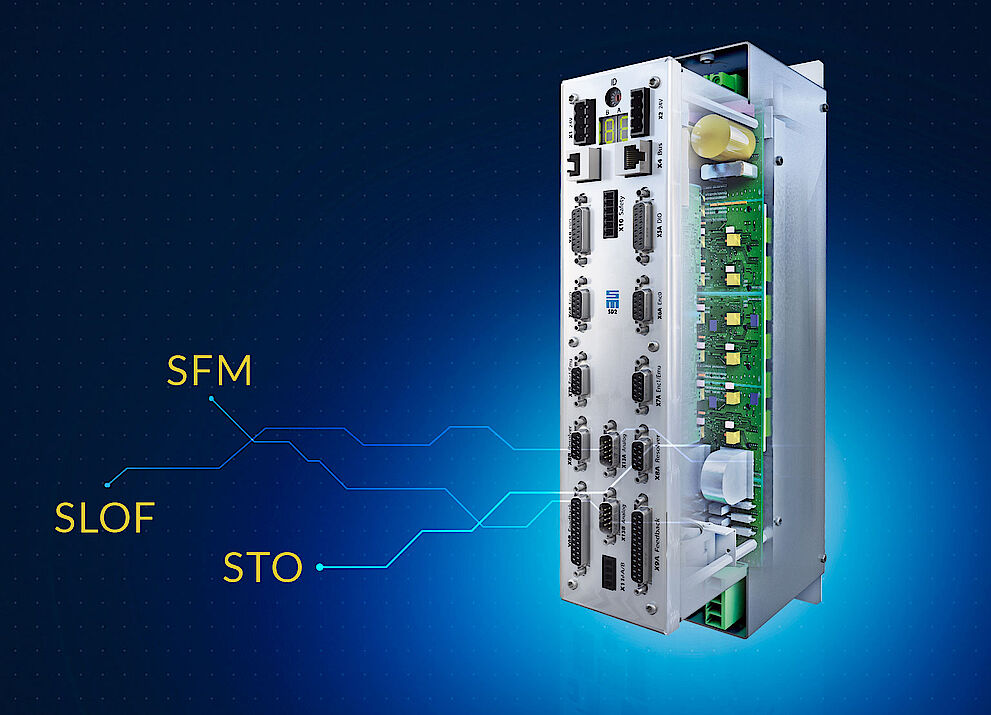
Drive Controller SD2 by SIEB & MEYER with Integrated Safety Functions
Feel free to contact us
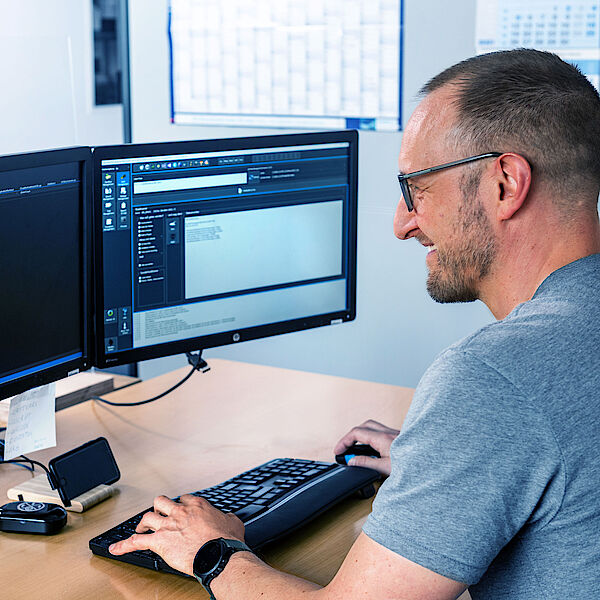
![[Translate to Englisch:] Antriebssystem SD2](/fileadmin/_processed_/d/7/csm_Header_SD2_434943ee7f.png)
Drive Controller SD2
The drive controller SD2 is designed to control synchronous and asynchronous motors with or without a sensor and permits quick and easy adaptation to the individual case of application – whether used with linear motors, rotary motors or motor-driven machining spindles.
This universal drive solution allows realization of high-speed applications up to 360,000 rpm (6,000 Hz). Universal motor encoder interfaces and different connection possibilities to a higher-ranking control allow easy adaptation to changing system requirements – nothing will stand in the way of the optimal realization of multi-axis applications.
Highlights
Multi-Axis System
- Function: The SD2 single and double drive controllers can be supplied by a common power supply unit
- Advantage: The DC voltage coupling allows recovering energy: The energy produced by the braking axes can be used by the driving axes. Depending on the system performance mains supply for up to 12 axis modules can be realized.
- Benefit: Low wiring and energy costs.
Load Indicator
- Function: SD2 offers a high-precision evaluation of the torque generating current by default.
- Advantage: The evaluation can be used for tool monitoring. These are for example detection of tool breakage, tool wear, gap eliminator (GAP and crash) and an optimal control of the feed rate during the manufacturing process.
- Benefit: Lower system costs, no need for cost-intensive monitoring sensors.
Safety Integrated
- Function: "Safe Torque Off" (STO) is integrated as standard in the device. The sensorless functions "Safe Frequency Monitor" (SFM) and "Safe Limited Output Frequency (SLOF) are available as options.
- Advantage: No need of external safety components while safety standards are met.
- Benefit: Minimization of system costs and higher machine availability.
The Team Player
As a standard all devices of series SD2 are equipped with "Safe Torque Off" (STO). The sensorless safety functions "Safe Frequency Monitor" (SFM) and "Safe Limited Output Frequency” (SLOF) are available as option.
This is a great benefit to allow compliance with the requirements of the Machinery Directive.
The Interfaces of SD2 (Two-channel Device)
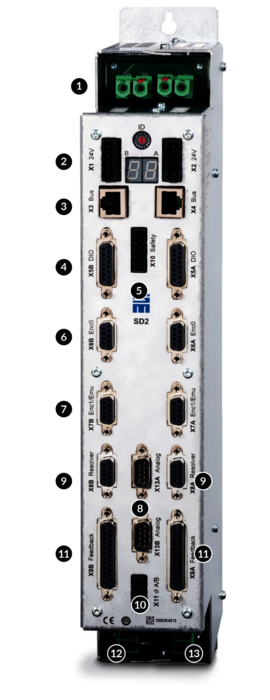
- Mains supply (DC)
- 24 V-Logic supply
- Parameterization and diagnosis
- 6 digital inputs and 4 digital outputs
- Safety integrated "STO": Restart lock to meet category 4/PL e according to EN ISO 13849-1:2015 and EN 61508:2010 SIL3
- Encoder inputs and outputs (Puls-direction signals)
- Encoder inputs and outputs (measuring system simulation)
- Analog reference value interfaces: +/-10 V
- Resolver inputs
- Thermal contacts
- Universal motor encoder interface: Encoder / linear scale(TTL or Sin/Cos), EnDat, Hiperface, SSI, Hall effect sensor, linearer Hall sensor, magnetoresistive sensor
- SERVOLINK 4 via optical fiber connector
- 2 x Motor connection for synchronous / asynchronous spindles, linear motors and rotary motors
EtherCAT, PROFIBUS and PROFINET via gateway
Drive Functions and Safety Functions
Software for Initial Operation and Parameterization: drivemaster2
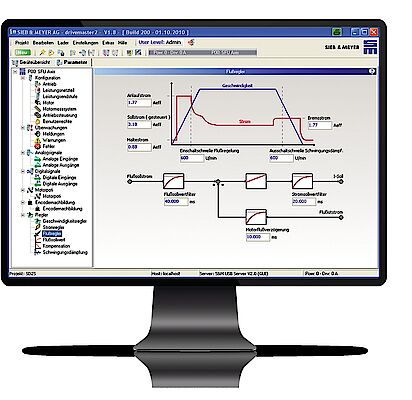
Parameterization
• Tree-type structure
• Block diagrams
• Graphics
• Interactive help messages
• Comments
• „Parameter-Wizard“
• Saving and reloading of projects, parameter files and motor parameters
• Centralized access to all axes
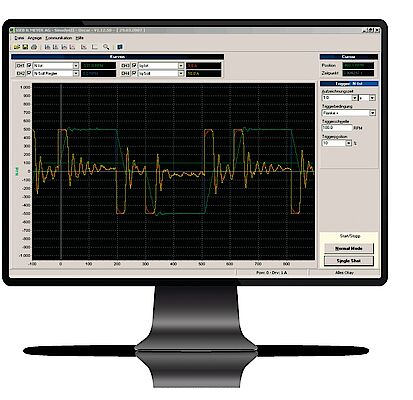
Diagnosis
• 4-channel oscilloscope
• Zoom functions
• Trigger functions
• Long-term recording function
• Measurements can be saved
• Diagnosis of the inputs and outputs
• Bus monitor
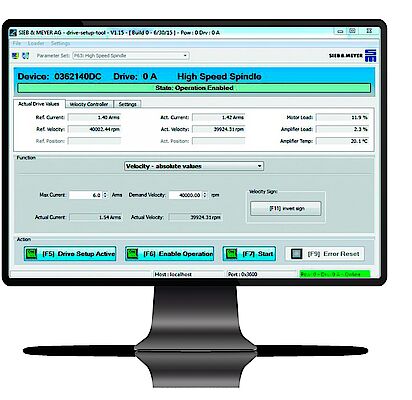
Operation
• Without higher-ranking control
• Visualized reference and actual values
• Error and status messages
Technical Specifications SD2 with Integrated Heat Sink
Device type | Rated power1 | Rated current | Peak current/time | Max. output voltage1 | HxWxD (mm) | Weight | Cooling |
---|---|---|---|---|---|---|---|
Single drive controller - 325 VDC supply voltage | |||||||
0362114IC | 8.6 kVA | 25 Arms | 56.6 Arms/2 s | 3 x 200 VAC | 410 x 70 x 207 | 5.7 kg | Air |
Single drive controller - 560...680 VDC supply voltage | |||||||
0362114EF | 9.9 kVA | 14 Arms | 28.3 Arms/2 s | 3 x 410 VAC | 410 x 70 x 207 | 5.7 kg | Air |
0362114IF | 9.9 kVA | 14 Arms | 56.6 Arms/2 s | 3 x 410 VAC | 410 x 70 x 207 | 5.7 kg | Air |
0362114MF | 24.8 kVA | 35 Arms | 113 Arms/2 s | 3 x 410 VAC | 410 x 130 x 207 | 9.3 kg | Air |
0362114NF | 24.8 kVA | 35 Arms | 141 Arms/2 s | 3 x 410 VAC | 410 x 130 x 207 | 9.3 kg | Air |
0362111RF | 78 kVA | 127 Arms | 177 Arms/25 s | 3 x 410 VAC | 390 x 230 x 144 | 8.7 kg | Water |
0362111SF | 141 kVA | 200 Arms | 245 Arms/25 s | 3 x 410 VAC | 410 x 230 x 180 | 11 kg | Water |
Double drive controller - 325 VDC supply voltage | |||||||
0362113EEC | 3.5 kVA + 3.5 kVA | 10 Arms + 10 Arms | 28.3 Arms/2 s + 28.3 Arms/2 s | 3 x 200 VAC | 410 x 70 x 207 | 5.7 kg | Air |
Double drive controller - 560...680 VDC supply voltage | |||||||
0362113CCF | 4.5 kVA + 4.5 kVA | 6,4 Arms + 6,4 Arms | 7,1 Arms/5 s + 7,1 Arms/5 s | 3 x 410 VAC | 249 x 70 x 232 | 5.7 kg | Air |
0362113EEF | 5 kVA + 5 kVA | 7 Arms + 7 Arms | 28,3 Arms/2 s + 28,3 Arms/2 s | 3 x 410 VAC | 249 x 70 x 232 | 5.7 kg | Air |
Double compact devices - (1)3 x 110...230 VDC mains voltage | |||||||
0362131DDC | 6.4 kVA | 11 Arms + 11 Arms | 14 Arms/5 s + 14 Arms/5 s | 3 x 200 VAC | 410 x 100 x 207 | 7.5 kg | Air |
0362131SSC | 6.4 kVA | 11 Arms + 11 Arms | 42 Arms/1 s + 42 Arms/1 s | 3 x 200 VAC | 410 x 100 x 207 | 7.5 kg | Air |
1) Rated power and max. output voltage for mains voltage/supply voltage (in italic)
SD2 with Integrated Heat Sink
Device type | Rated power1 | Rated current | Peak current/time | Max. output voltage1 | HxWxD (mm) | Weight | Cooling |
---|---|---|---|---|---|---|---|
Double compact devices - 3 x 400...480 VDC mains voltage | |||||||
362131DDF | 11.2 kVA | 7 Arms+ 7 Arms | 42 Arms/1 s + 42 Arms/1 s | 3 x 410 VAC | 410 x 100 x 207 | 7.5 kg | Air |
Technical Specifications of PS2 Power Supply Unit with Integrated Heat Sink
Device type | Rated power1 | HxWxD (mm) | Weight | Cooling |
---|---|---|---|---|
Power supply unit - 3 x 110...480 VAC mains voltage | ||||
0362191F | 27 kW | 410 x 70 x 207 | 5.8 kg | Air |
0362193F | 72 kW | 410 x 160 x 207 | 9.35 kg | Air |
1) Rated power and max. output voltage for mains voltage/supply voltage (in italic)
Technical Specifications of SD2 with Integrated Heat Sink and Safety Functions SFM/SLOF
Device type | Rated power1 | Rated current | Peak current/time | Max. output voltage1 | HxWxD (mm) | Weight | Cooling |
---|---|---|---|---|---|---|---|
Single drive controller - 560...680 VDC supply voltage | |||||||
0362314DF | 8 kVA | 11.3 Arms | 14.1 Arms/5 s | 3 x 410 VAC | 410 x 70 x 209 | 5.7 kg | Air |
0362414EF | 14.2 kVA | 20 Arms | 28.3 Arms/2 s | 3 x 410 VAC | 410 x 70 x 209 | 5.7 kg | Air |
0362414QF | 30 kVA | 42 Arms | 85 Arms/2 s | 3 x 410 VAC | 415 x 135 x 218 | 7.0 kg | Air |
0362414RF | 85 kVA | 120 Arms | 177 Arms/15 s | 3 x 410 VAC | 410 x 103 x 209 | 6.5 kg | Air |
Double drive controller - 560...680 VDC supply voltage | |||||||
0362413DDF | 6.4 kVA + 6.4 kVA | 9 Arms + 9 Arms | 14 Arms/5 s + 14 Arms/5 s | 3 x 410 VAC | 410 x 70 x 207 | 5.7 kg | Air |
1) Rated power and max. output voltage for mains voltage/supply voltage (in italic)
2) Output power at three-phase mains
Device type | Rated power1 | Rated current | Peak current/time | Max. output voltage1 | HxWxD (mm) | Weight | Cooling |
---|---|---|---|---|---|---|---|
Single drive controller - 680 VDC supply voltage | |||||||
0362111EF | 7.8 kVA | 11 Arms | 28 Arms/2 s | 3 x 410 VAC | 410 x 70 x 134 | 3 kg | Cold-Plate |
0362111IF | 11.4 kVA | 16 Arms | 56 Arms/1 s | 3 x 410 VAC | 410 x 70 x 134 | 3 kg | Cold-Plate |
0362111NF | 24.8 kVA | 35 v | 141 Arms/2 s | 3 x 410 VAC | 410 x 130 x 134 | 9 kg | Cold-Plate |
Double drive controller - 680 VDC supply voltage | |||||||
0362110DDF | 7.8 kVA + 7.8 kVA | 11 Arms + 11 Arms | 14 Arms/5 s + 14 Arms/5 s | 3 x 410 VAC | 410 x 70 x 134 | 3 kg | Cold-Plate |
0362110EEF | 7.8 kVA + 7.8 kVA | 11 Arms + 11 Arms | 28 Arms/5 s + 28 Arms/5 s | 3 x 410 VAC | 410 x 70 x 134 | 3 kg | Cold-Plate |
Double compact devices - (1)3 x 110...230 VDC mains voltage | |||||||
0362130SSC | 6.4 kVA | 11 Arms + 11 Arms | 42 Arms/1 s + 42 Arms/1 s | 3 x 200 VAC | 410 x 100 x 207 | 7.5 kg | Cold-Plate |
Double compact devices - 3 x 400...480 VDC mains voltage | |||||||
0362130DDF | 11.2 kVA | 7 Arms + 7 Arms | 14 Arms/5 s + 14 Arms/5 s | 3 x 410 VAC | 410 x 100 x 207 | 7.5 kg | Cold-Plate |
0362130SSF | 11.2 kVA | 7 Arms + 7 Arms | 42 Arms/1 s + 42 Arms/1 s | 3 x 410 VAC | 410 x 100 x 207 | 7.5 kg | Cold-Plate |
1) Rated power and max. output voltage for mains voltage/supply voltage (in italic)
Applications
About SIEB & MEYER
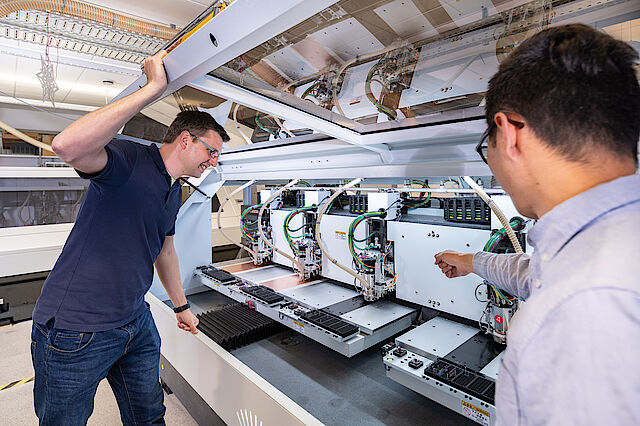
SIEB & MEYER AG - Drive and control solutions of the latest generation
SIEB & MEYER was founded in 1962 and is a successful company in the field of industrial electronics. With around 260 employees worldwide today, we develop and manufacture control technology and drive electronics. Our core technologies include controllers for mechanical engineering and automation technology, servo amplifiers for a wide range of drives and frequency converters for high-speed motors and generators.
Contact
SIEB & MEYER AG
Auf dem Schmaarkamp 21
D-21339 Lüneburg
Phone: +49 4131 203 0
Fax: +49 4131-203 2000
You can find all sales contacts at: www.sieb-meyer.com/contact/sales
You can find all agencies and partners at: www.sieb-meyer.com/contact/offices-and-sales-partners