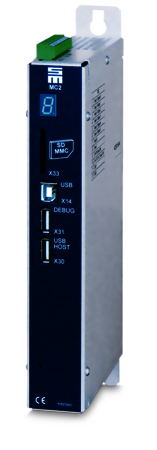
Motion Controller MC2
The drive system MC2 – including motion controller MC2 and drives of the series SD2S – is the solution for machine manufacturers who develop a PC-based application software and look for a well-proven system for the motion tasks. The communication between the motion controller MC2 and the client‘s PC is established via Ethernet based on the DNC-361 protocol.
Using the provided documentation the client can easily implement the protocol into his application software. Then, the various motion functions of the drive system MC2 are available in the application software.
The Motion Controller for Your Machine
MC2 runs a real-time operating system that permits synchronous data transmission to the drive amplifiers. This makes controlled spatial movement of the axes possible. The used optical fiber connection ensures an extremely fail-safe data line. As an option, MC2 also offers an EtherCAT master interface which enables direct data exchange between the MC2 and the application unit, e.g. an exposure unit.
The drive amplifiers SD2S can evaluate all common measuring systems and reach an exceptional positioning accuracy with very constant speed of the X/Y main axes. In addition, SD2B plus is available for Z-axis positioning, e.g. for focus adjustment of exposure units. These features ensure a high quality of the manufactured products. As an option, SD2S provides the opportunity to output trigger signals for the synchronization of the application unit, e.g. print head.
This function also allows scaling the motion axes to the resolution of the application unit. MC2 provides up to eight inputs or outputs for your machine.
With an optional, external I/O module the inputs and outputs can be expanded to a maximum of 96 inputs and 96 outputs. The transmission protocol IO-Link 3 ensures reliable data transmission to the I/O system 50.06 via optical fiber cables.
System Specifications of the Drive System:
- Ethernet interface with DNC-361 protocol (UDP telegrams)
- Point-to-point control, position interpolation points
- Linear and circular interpolation
- Gantry, gear function
- Scalable trigger function (optional)
- Internal resolution up to 20 nm (standard 100 nm)
- Very precise synchronization
- Parameterization and optimization via software drivemaster2 and drivemaster3
- EtherCAT master-interface
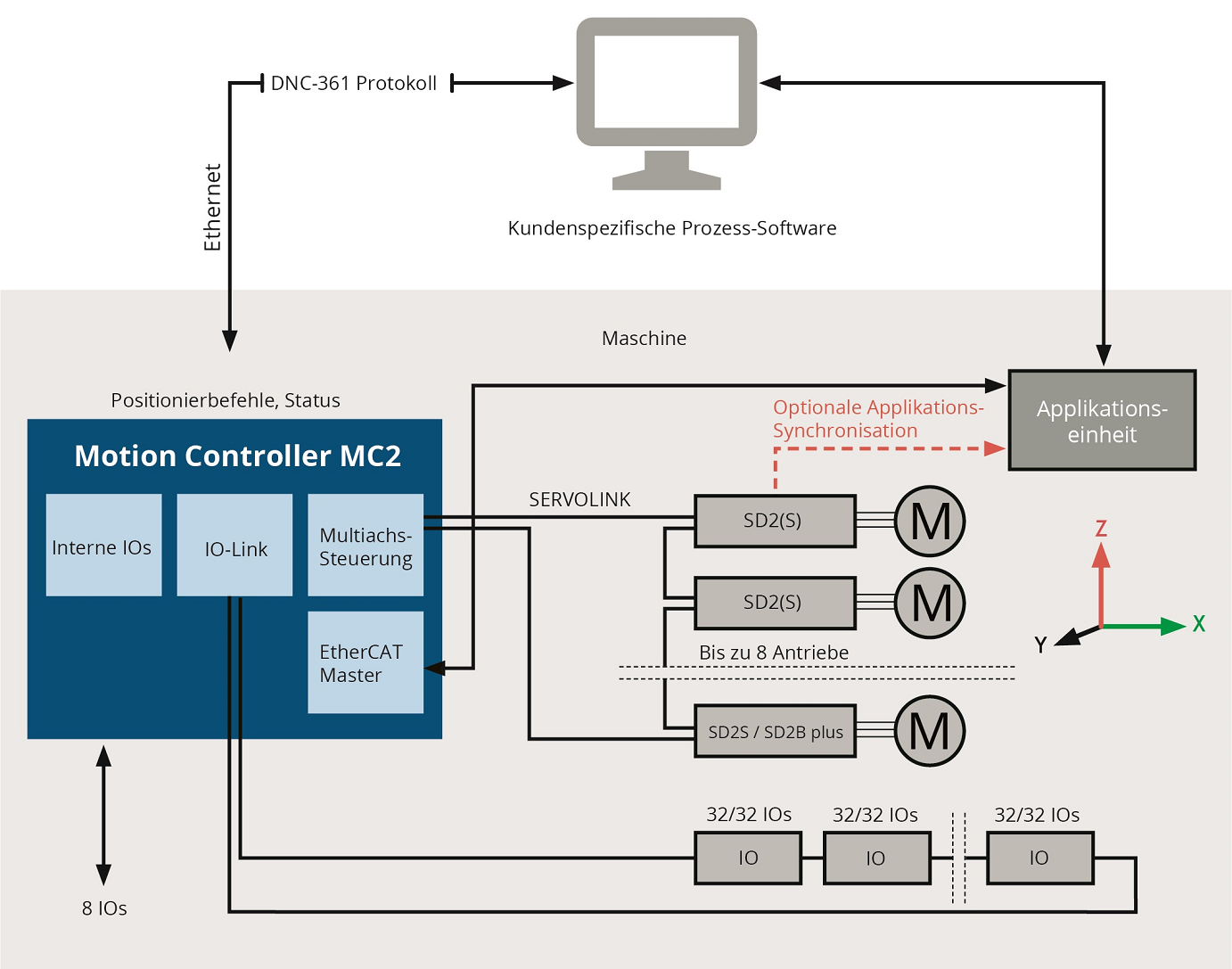
Software for initial operation and parameterization: drivemaster2/drivemaster3
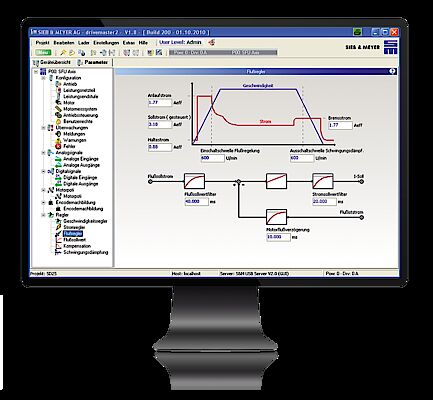
drivemaster2/drivemaster3 is a powerful tool for easy and goal-oriented parameterization and optimization of drive axes. The parameters are used to adapt the drive axes to the mechanical and electrical characteristics of the machine.
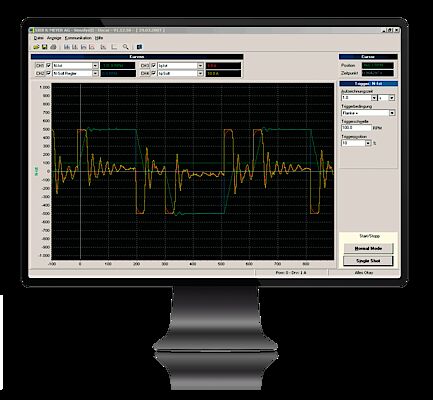
OSCAR is an auxiliary program for optimizing machine movements. By means of the graphic visualization speeds, accelerations, and moving characteristics can be set individually for each axis. With this online optimization the machine manufacturer can determine the best possible values for a machine and thus achieve considerable improvements in the machine´s productivity.
Technical Details of MC2/SD2S/SD2B plus
Motion Controller MC2
- nanoETX board
- Ethernet interface to the PC
- digital bus SERVOLINK via optical fibers to the drives SD2S and via IO-Link to the I/O system 50.06
- 8 inputs and outputs
- EtherCAT master interface
Servo Drive SD2S / SD2B plus
- servo drive for rotary and linear AC servo motors
- evaluation of incremental encoders, absolute or linear measuring systems
- digital bus via optical fibers for the connection with MC2
→ to the technical details of SD2S
→ to the technical details of SD2B plus
Decentral I/O System 50.06
- +24 VDC supply
- up to 96 inputs and 96 outputs
- inputs: +24 V (high active)
- outputs: +24 V / 350 mA
- CRC-controlled data transmission
Feel free to contact us
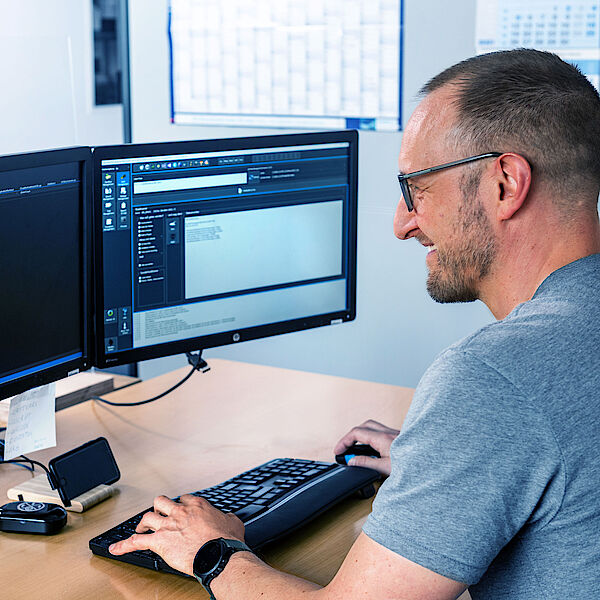
![[Translate to Englisch:] Motion Controller MC2](/fileadmin/_processed_/d/6/csm_Header_MC2_00bd1074d5.png)
Motion Controller MC2
The drive system MC2 – including motion controller MC2 and drive amplifiers of the series SD2S – is the solution for machine manufacturers who develop a PC-based application software and look for a well-proven system for the motion tasks. The communication between the motion controller MC2 and the client‘s PC is established via Ethernet based on the DNC-361 protocol.
Using the provided documentation the client can easily implement the protocol into his application software. Then, the various motion functions of the drive system MC2 are available in the application software.
The Motion Controller for Your Machine
MC2 runs a real-time operating system that permits synchronous data transmission to the drive amplifiers. This makes controlled spatial movement of the axes possible. The used optical fiber connection ensures an extremely fail-safe data line. As an option, MC2 also offers an EtherCAT master interface which enables direct data exchange between the MC2 and the application unit, e.g. an exposure unit.
The drive amplifiers SD2S can evaluate all common measuring systems and reach an exceptional positioning accuracy with very constant speed of the X/Y main axes. In addition, SD2B plus is available for Z-axis positioning, e.g. for focus adjustment of exposure units. These features ensure a high quality of the manufactured products. As an option, SD2S provides the opportunity to output trigger signals for the synchronization of the application unit, e.g. print head.
This function also allows scaling the motion axes to the resolution of the application unit. MC2 provides up to eight inputs or outputs for your machine.
With an optional, external I/O module the inputs and outputs can be expanded to a maximum of 96 inputs and 96 outputs. The transmission protocol IO-Link 3 ensures reliable data transmission to the I/O system 50.06 via optical fiber cables.
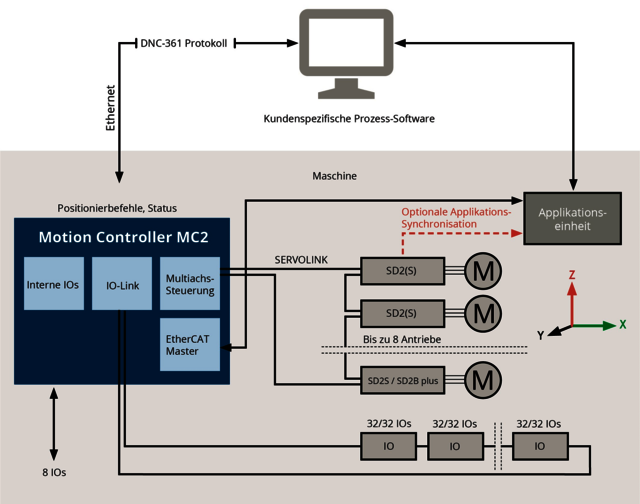
System Specifications of the Drive System:
- Ethernet interface with DNC-361 protocol (UDP telegrams)
- Point-to-point control, position interpolation points
- Linear and circular interpolation
- Gantry, gear function
- Scalable trigger function (optional)
- Internal resolution up to 20 nm (standard 100 nm)
- Very precise synchronization
- Parameterization and optimization via software drivemaster2 and drivemaster3
- EtherCAT master-interface
Software for initial operation and parameterization:
drivemaster2/drivemaster3
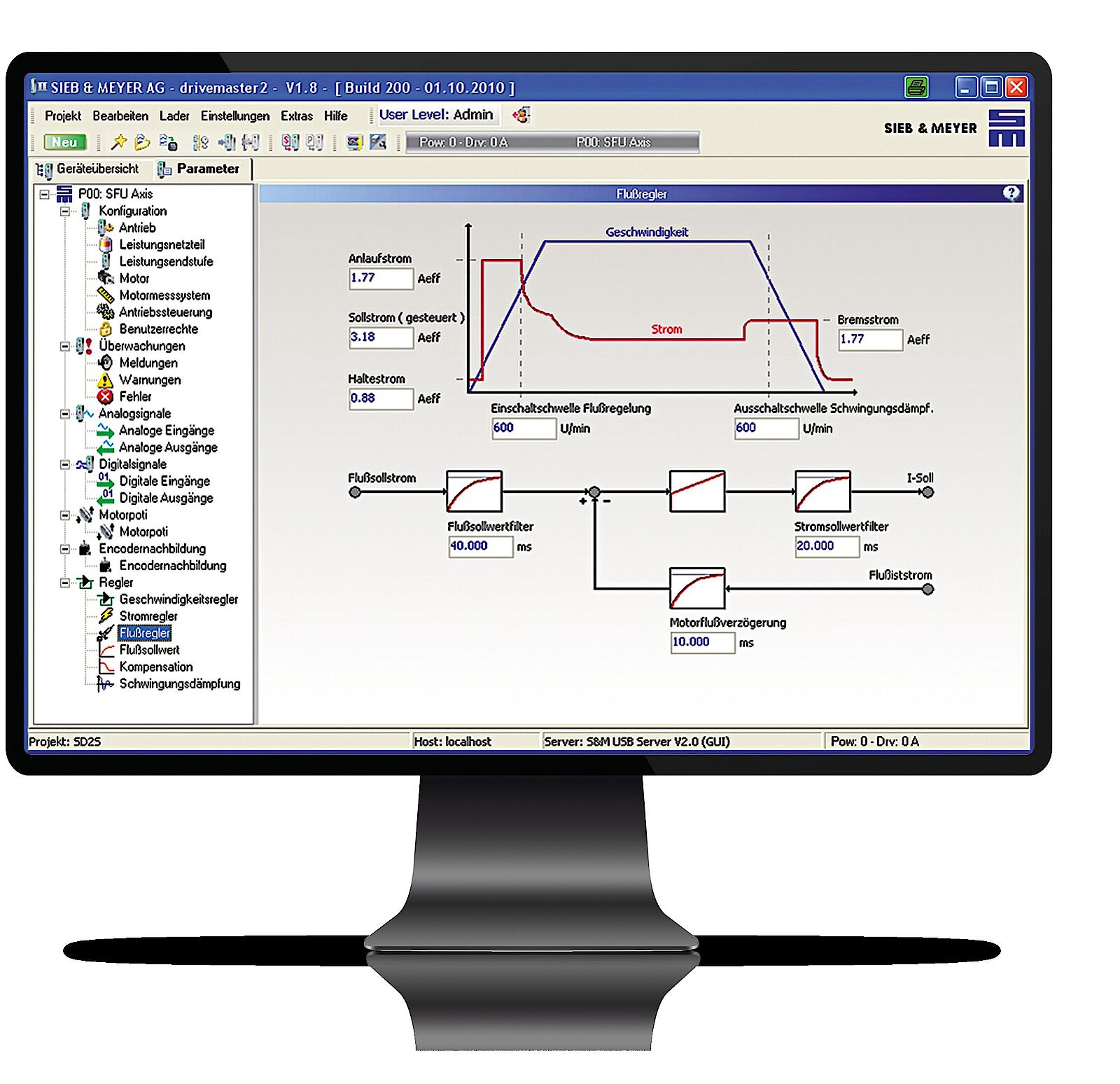
drivemaster2/drivemaster3 is a powerful tool for easy and goal-oriented parameterization and optimization of drive axes. The parameters are used to adapt the drive axes to the mechanical and electrical characteristics of the machine.
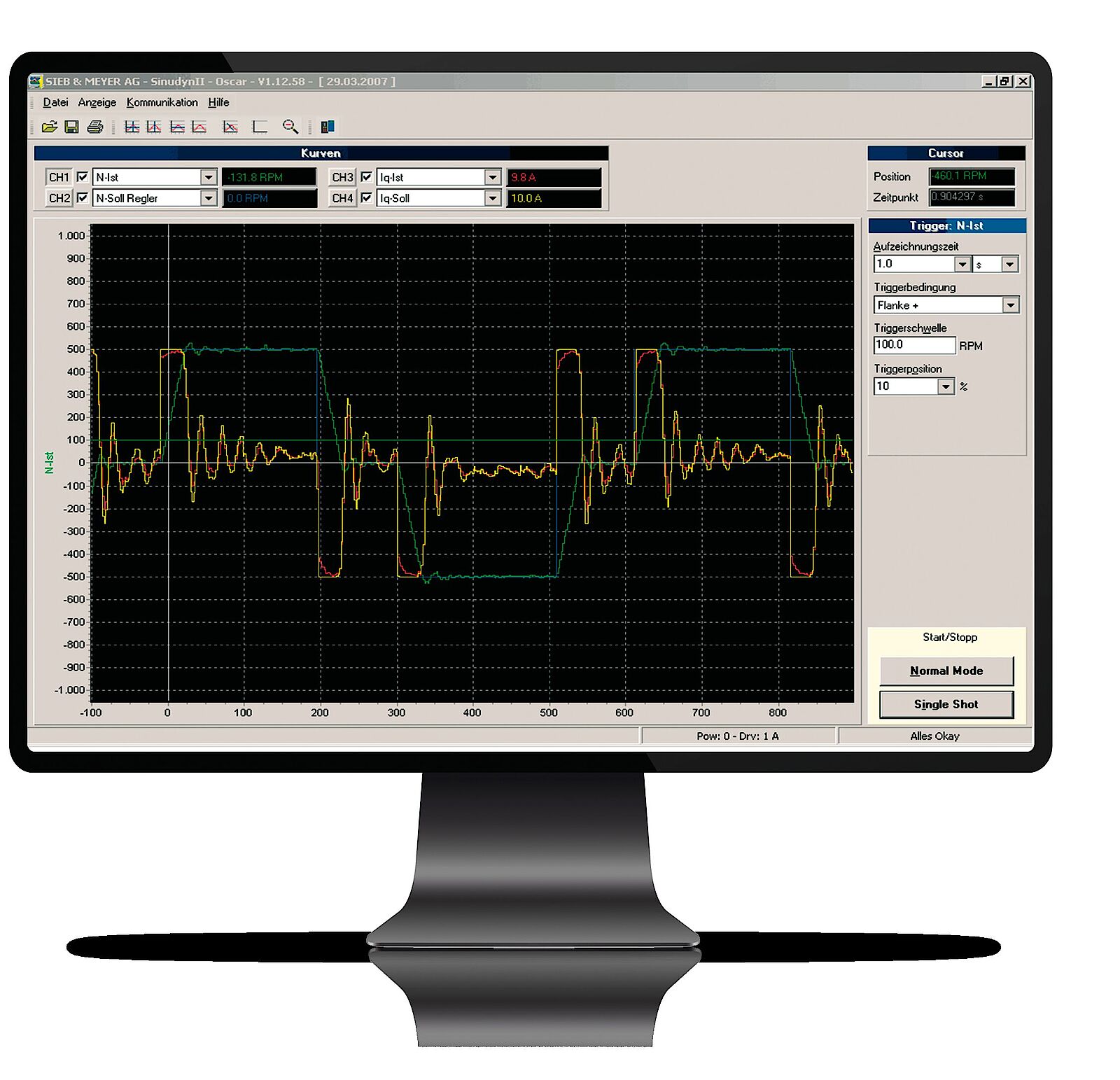
OSCAR is an auxiliary program for optimizing machine movements. By means of the graphic visualization speeds, accelerations, and moving characteristics can be set individually for each axis. With this online optimization the machine manufacturer can determine the best possible values for a machine and thus achieve considerable improvements in the machine´s productivity.
Technical Detals of MC2/SD2S/SD2B plus
Motion Controller MC2
• nanoETX board
• Ethernet interface to the PC
• digital bus SERVOLINK via optical fibers to the drives SD2S and via IO-Link to the I/O system 50.06
• 8 inputs and outputs
• EtherCAT master interface
Servo Amplifier
SD2S / SD2B plus
• servo amplifier for rotary and linear AC servo motors
• evaluation of incremental encoders, absolute or linear measuring systems
• digital bus via optical fibers for the connection with MC2
Decentral I/O System 50.06
• +24 VDC supply
• up to 96 inputs and 96 outputs
• inputs: +24 V (high active)
• outputs: +24 V / 350 mA
• CRC-controlled data transmission
Applications
About Sieb & Meyer
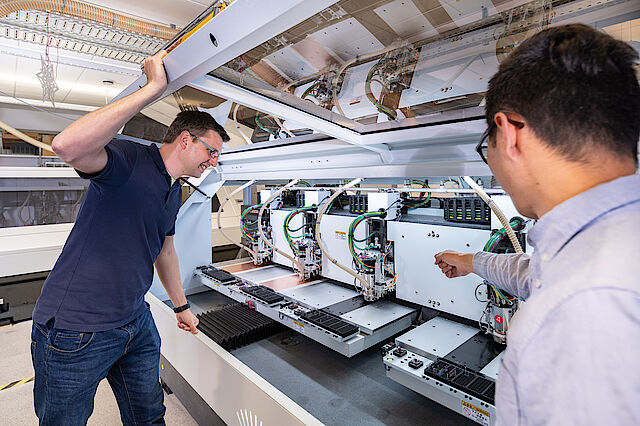
SIEB & MEYER AG - Drive and control solutions of the latest generation
SIEB & MEYER was founded in 1962 and is a successful company in the field of industrial electronics. With around 300 employees worldwide today, we develop and manufacture control technology and drive electronics. Our core technologies include controllers for mechanical engineering and automation technology, servo amplifiers for a wide range of drives and frequency converters for high-speed motors and generators.
Contact
SIEB & MEYER AG
Auf dem Schmaarkamp 21
D-21339 Lüneburg
Phone: +49 4131 203 0
Fax: +49 4131-203 2000
You can find all sales contacts at: www.sieb-meyer.com/contact/sales
You can find all agencies and partners at: www.sieb-meyer.com/contact/offices-and-sales-partners