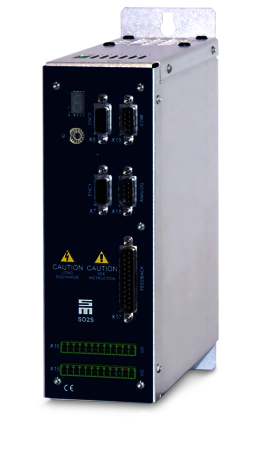
Frequency Converter SD2S-FPAM
Highest speeds, lowest motor heating and best control performance – always in real time: The technical basis is the controlled intermediate DC circuit combined with the established pulse-amplitude modulation (PAM) which allows SD2S doing without additional motor chokes even at high speeds.
Based on this technology SIEB & MEYER developed two extremely robust and sensorless control methods: V/f-PAM for asynchronous motors and FPAM for synchronous motors. The usually very special applications in this area require close coordination between the user and SIEB & MEYER. Applications with a large variance of engine types (such as engine test stations) are rather unsuitable.
Highlights
Device Topology
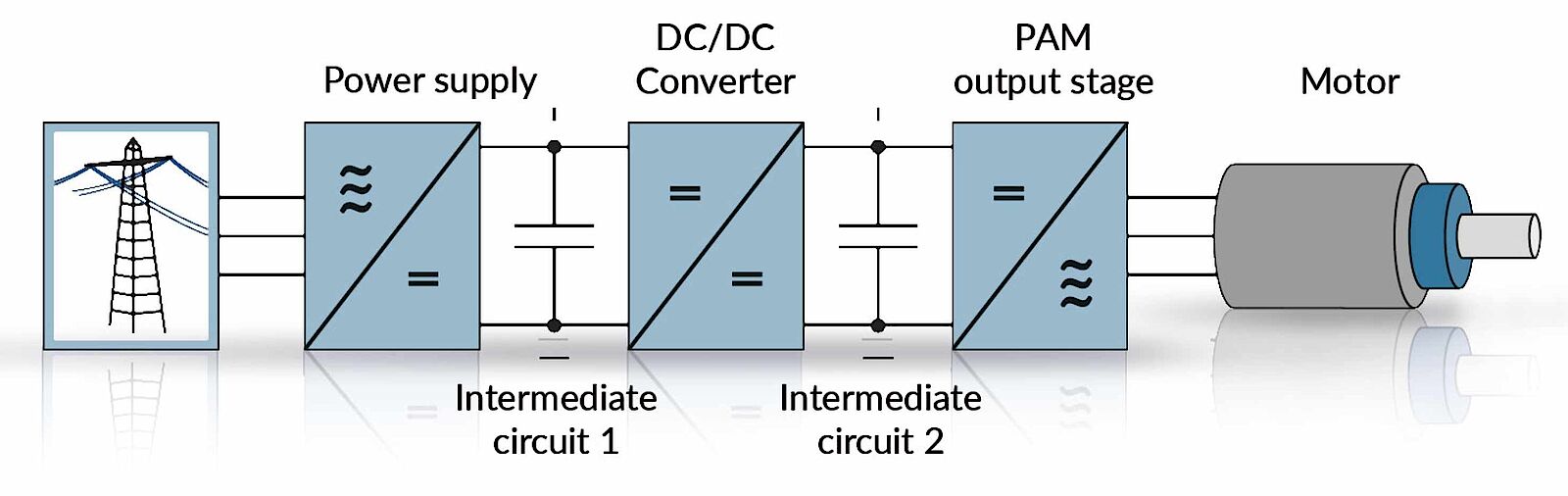
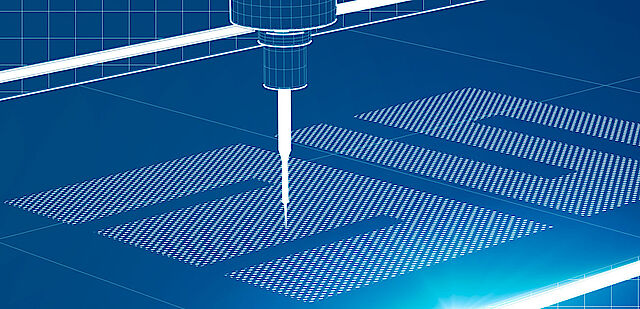
The Fast One
The existing standard SD2S-FPAM devices are also used as technical basis for customized devices. This way, the customer obtains an optimal solution that is individually adapted to the specific application.
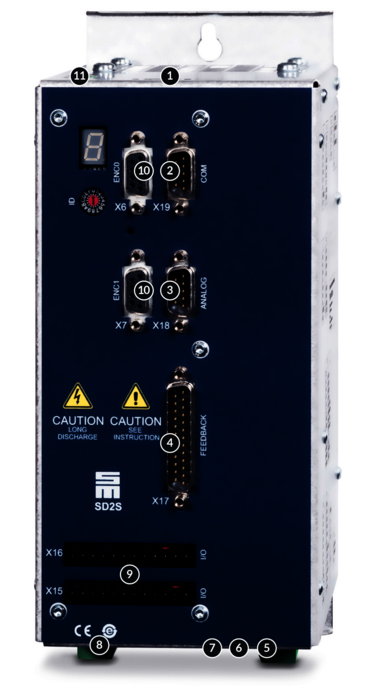
The Interfaces of Frequency Converter SD2S-FPAM
- USB connection, parameterization, diagnosis and operation
- RS232 / CAN interface
- 2 analog reference value interfaces: +/-10 V;
2 analog outputs: 0 - 10 V - Universal motor encoder interface:
Hall sensor, linear Hall sensor, magnetoresistive sensor, NAMUR sensor (pulse generator), Sin/Cos encoder - Motor connection
- Optional: EtherCAT (CoE)
- SERVOLINK 4 via optical fiber PROFIBUS adapter
- Power supply
- 9 digital inputs and 5 digital outputs
- 2 TTL encoder inputs and outputs
- Safety Intergrated "STO": Restart lock to meet category 4/PL e according to EN ISO 13849-1:2015 and EN 61508:2010 SIL
PROFIBUS and PROFINET via gateway
Drive Functions and Safety Functions
Software for Initial Operation and Parameterization: drivemaster2
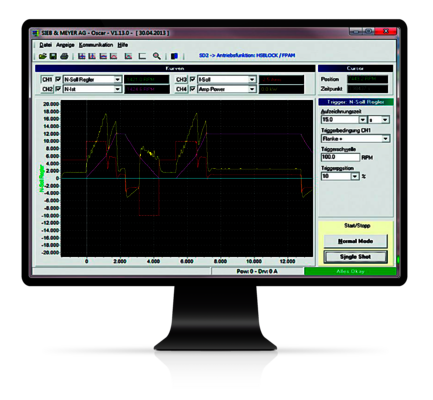
The oscilloscope function allows optimization of the axes in the machine via the drive-setup-tool without additional measuring equipment.
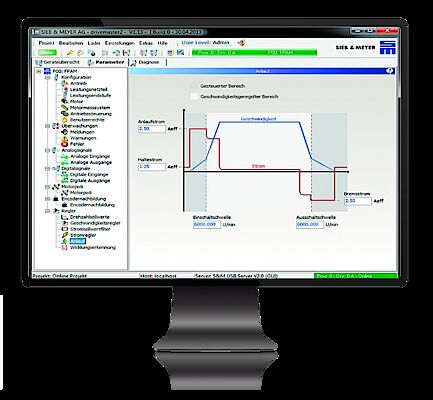
The clear design of the software allows intuitive parameterization via graphics and block diagrams. The „Parameter-Wizard“ guides the user step-by-step through the system configuration and allows intuitive setup of the device via help messages and comments.

Operation Unit (optional)
LCD status display for the indication of operating data:
- Parameters
- Reference / actual speed
- Load display
- Active spindle
- Error messages
LED status displays for:
- Ready for operation
- Load message
Technical Specifications of Frequency Converter SD2S-FPAM
Device type | Rated power1 | Rated current | Peak current/time | Max. output voltage1 | HxWxD (mm) | Weight | Cooling |
---|---|---|---|---|---|---|---|
Compact devices - 1 x 110...230 VAC mains voltage | |||||||
0362X42DC | 1.5 kVA | 10 Arms | 14 Arms/2 s | 3 x 200 VAC | 280 x 75 x 230 | 3 kg | Air |
Compact devices - 1(3) x 110...230 VAC mains voltage | |||||||
0362X42EC | 3.8 kVA | 10 Arms | 28 Arms/2 s | 3 x 200 VAC | 253 x 104 x 188 | 4 kg | Air |
X = 1: CAN bus
X = 2: EtherCAT and CAN Bus
1) Rated power and max. output voltage for mains voltage/supply voltage (in italic)
Feel free to contact us
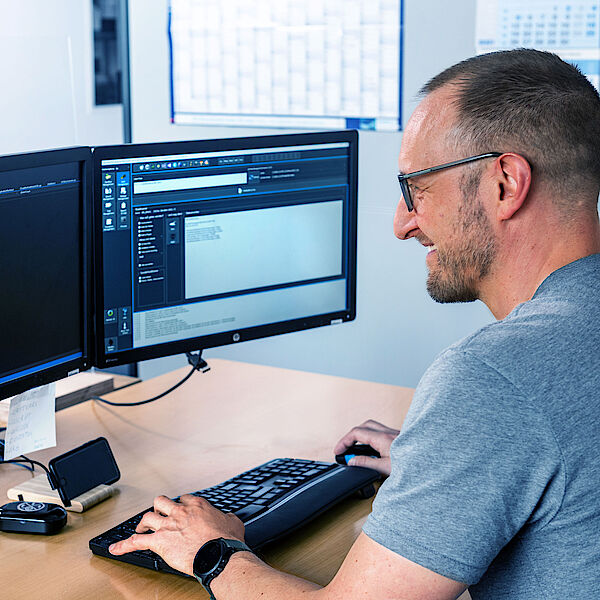
![[Translate to Englisch:] Frequenzumrichter SD2S-FPAM](/fileadmin/_processed_/f/0/csm_Header_SD2S_FPAM_a67ffbdae9.png)
Frequency Converter SD2S-FPAM
Highest speeds, lowest motor heating and best control performance – always in real time: The technical basis is the controlled intermediate DC circuit combined with the established pulse-amplitude modulation (PAM) which allows SD2S doing without additional motor chokes even at high speeds.
Based on this technology SIEB & MEYER developed two extremely robust and sensorless control methods: V/f-PAM for asynchronous motors and FPAM for synchronous motors. The usually very special applications in this area require close coordination between the user and SIEB & MEYER. Applications with a large variance of engine types (such as engine test stations) are rather unsuitable.
Highlights
Output Frequencies
up to 8,000 Hz
- Function: Established PAM technology with optimized dynamic characteristics, efficiency and flexibility.
- Advantage: Virtually no speed limitation combined with optimized control dynamics and excellent system efficiency.
- Benefit: Low initial costs, possibility to access new applications.
Sensorless Control of Synchronous and Asynchronous Motors
- Function: The control of synchronous motors (FPAM) is based on the accurate EMF measurement in accordance to the rotor position. For asynchronous motors the well-proven drive function V/f-PWM is used.
- Advantage: Cost-intensive speed sensors are not required. Flexible switching from synchronous to asynchronous motors is possible.
- Benefit: Cost savings, easy initial operation.
No Need of Motor Chokes
or LC-Filters
- Function: The PAM technology allows smallest switching frequencies and reduces the electric stress of the motor as well as interferences (EMC) significantly.
- Advantage: Additional filter elements or motor chokes are not required.
- Benefit: Low system costs, easy initial operation.
Device Topology
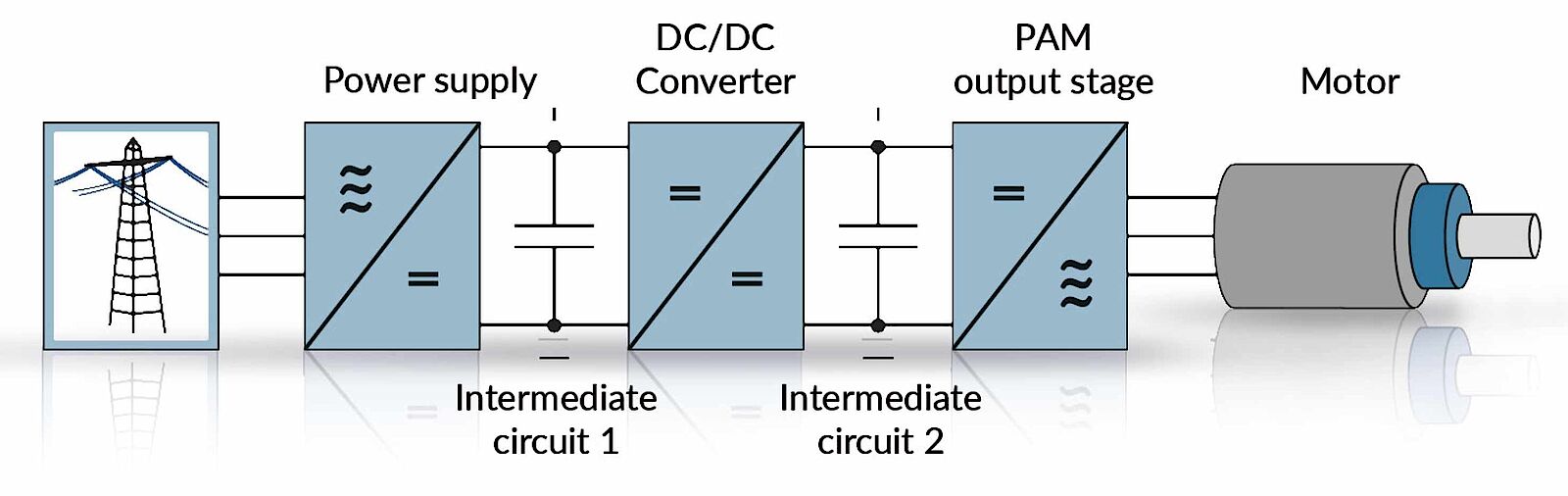
The Fast One
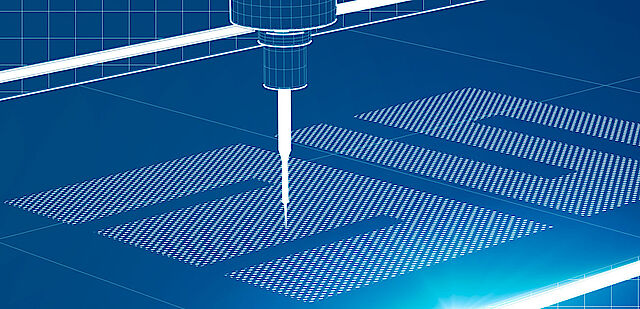
The existing standard SD2S-FPAM devices are also used as technical basis for customized devices.
This way, the customer obtains an optimal solution that is individually adapted to the specific application.
The Interfaces of Frequency Converter SD2S-FPAM
![2500x2500_technische-Details_SD2S_FPAM_01.png [Translate to Englisch:] Frequenzumrichter SD2S-FPAM](/fileadmin/_processed_/a/5/csm_2500x2500_technische-Details_SD2S_FPAM_01_e1835acba6.png)
- USB connection, parameterization, diagnosis and operation
- RS232 / CAN interface
- 2 analog reference value interfaces: +/-10 V;
2 analog outputs: 0 - 10 V - Universal motor encoder interface:
Hall sensor, linear Hall sensor, magnetoresistive sensor, NAMUR sensor (pulse generator), Sin/Cos encoder - Motor connection
- Optional: EtherCAT (CoE)
- SERVOLINK 4 via optical fiber PROFIBUS adapter
- Power supply
- 9 digital inputs and 5 digital outputs
- 2 TTL encoder inputs and outputs
- Safety Intergrated "STO": Restart lock to meet category 4/PL e according to EN ISO 13849-1:2015 and EN 61508:2010 SIL
PROFIBUS and PROFINET via gateway
Drive Functions and Safety Functions
Inbetriebnahme- und Parametriersoftware: drivemaster2
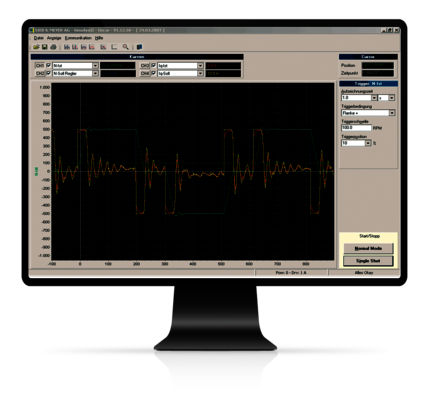
The oscilloscope function allows optimization of the axes in the machine via the drive-setup-tool without additional measuring equipment.
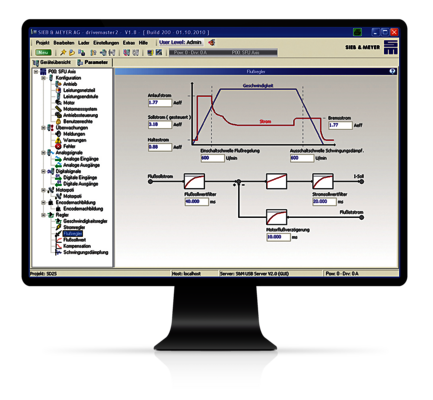
The clear design of the software allows intuitive parameterization via graphics and block diagrams. The „Parameter-Wizard“ guides the user step-by-step through the system configuration and allows intuitive setup of the device via help messages and comments.
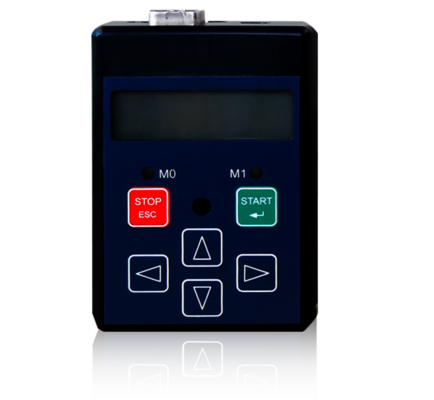
Operation Unit (optional)
LCD status display for the indication of operating data:
- Parameters
- Reference / actual speed
- Load display
- Active spindle
- Error messages
LED status displays for:
- Ready for operation
- Load message
Technical Specifications of Frequency Converter SD2S-FPAM
Device type | Rated power1 | Rated current | Peak current/time | Max. output voltage1 | HxWxD (mm) | Weight | Cooling |
---|---|---|---|---|---|---|---|
Compact devices - 1 x 110...230 VAC mains voltage | |||||||
0362X42DC | 1.5 kVA | 10 Arms | 14 Arms/2 s | 3 x 200 VAC | 280 x 75 x 230 | 3 kg | Air |
Compact devices - 1(3) x 110...230 VAC mains voltage | |||||||
0362X42EC | 3.8 kVA | 10 Arms | 28 Arms/2 s | 3 x 200 VAC | 253 x 104 x 188 | 4 kg | Air |
X = 1: CAN bus
X = 2: EtherCAT and CAN Bus
1) Rated power and max. output voltage for mains voltage/supply voltage (in italic)
Applications
About Sieb & Meyer
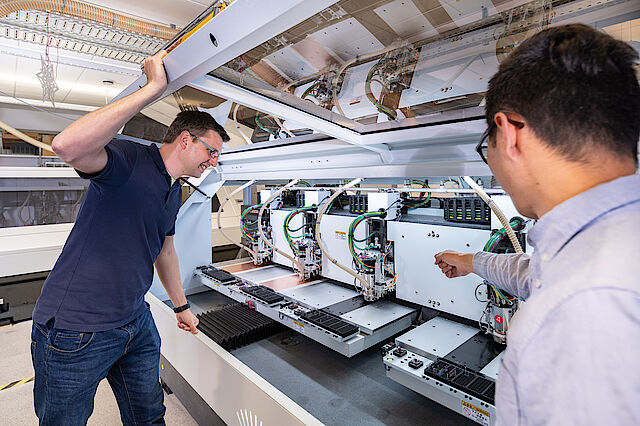
SIEB & MEYER AG - Drive and control solutions of the latest generation
SIEB & MEYER was founded in 1962 and is a successful company in the field of industrial electronics. With around 300 employees worldwide today, we develop and manufacture control technology and drive electronics. Our core technologies include controllers for mechanical engineering and automation technology, servo amplifiers for a wide range of drives and frequency converters for high-speed motors and generators.
Contact
SIEB & MEYER AG
Auf dem Schmaarkamp 21
D-21339 Lüneburg
Phone: +49 4131 203 0
Fax: +49 4131-203 2000
You can find all sales contacts at: www.sieb-meyer.com/contact/sales
You can find all agencies and partners at: www.sieb-meyer.com/contact/offices-and-sales-partners