OPC UA as Standard Data Interface
Technical papers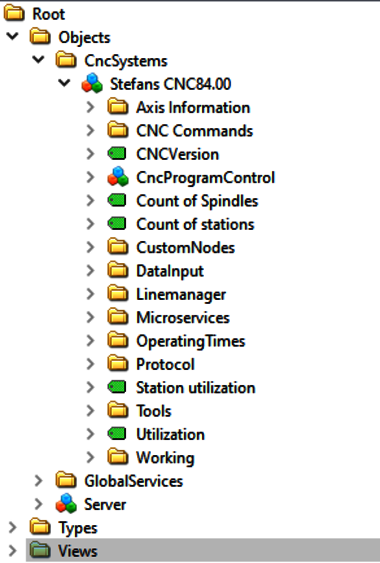
for SIEB & MEYER CNC Controls
SIEB & MEYER has equipped its CNC controls for PCB production with a standardized interface in order to be open for future requirements. OPC UA is the future standard interface in the CNC 93.00 and CNC 95.00 controls.
Communication structures and a uniform language are necessary if people want to communicate across cultures and continents. The international language Esperanto follows this approach and was published in 1887 for the first time. The modern industrial environment of the 21st century deals with a similar challenge.
SIEB & MEYER is one of the world's largest providers of CNC controls in the field of PCB processing (drilling and routing). For many years now, the company has been familiar with connecting its own products to systems of third-party providers. These may be e.g. DNC servers for providing process parameters such as machine-specific part programs, tool data and production parameters as well as MES and ERP systems. As in many other sectors, these interfaces were grown over a long period of time and continuously developed. They serve to meet the sector's specific requirements and hence can be referred to as proprietary. A universal industrial standard did not exist up to now.
In the last years the demand for efficient optimization and flexible production processes rapidly increased in the field of PCB processing. The requirements include:
- efficient production planning
- 1-piece manufacturing: self-describing product
- predictive maintenance
- collection and analysis of measurement data
- process automation
In general, these requirements can be summed up in one term as "Industry 4.0". This goal can only be achieved with an integrated networking of all components. Just as important are standardized communication interfaces from company level (ERP) down to the field level including e.g. CNC controls by SIEB & MEYER.
This is why SIEB & MEYER equipped its CNC controls with a standardized interface to address future demands. Market analyses have shown that OPC UA has taken on an increasingly significant role as M2M communication standard in different sectors. This has been the main task of the Lueneburg-based company. The focus is not only a standardized and future-oriented data interface, but also a robust and stable solution for reliable 24/7 operations.
The service-based OPC UA communication protocol (OPC Unified Architecture) is the successor of the classic OPC standard. The OPC UA standard allows for machine data to be described and exchanged independent from manufacturers and platforms. Thus, it is possible to make data available between all connected systems of a company.
The OPC UA interface is used to forward data between the client and the server during runtime. The OPC UA server displays variable names and types as well as many different objects with any information and their relationships to each other. Functions such as historical data or alarms can be defined based on names, values, attributes, methods and events. An object is for example a control mechanism for the wear rate of a drill with a hit counter, alarm parameters and alarm limits.
The OPC UA standard is defined by the OPC Foundation (IEC 62541) and has been realized by SIEB & MEYER as follows:
- basic data types, system of units and transfer protocols
- access to data (DA)
- historical data (HA)
- alarms and messages (AC)
OPC UA is device-independent. Several standard tools for handling the data provided by an OPC UA server are available on the market. The tools can be connected directly to the OPC UA servers of our CNC controls. The knowledge of the OPC UA standard is sufficient to enable data communication with the CNCs. Thanks to the OPC UA standard libraries available in different programming languages (e.g. C#, Python, Node.js), it is easy to realize automation processes. A specific know-how of proprietary interfaces is not necessary anymore and the user can fully focus on the data and its processing.
The idea behind OPC UA is to represent each device in an own data model. This model is self-describing and can be published via an OPC UA server. The following was implemented by SIEB & MEYER: Each CNC control provides its own data model. The model can be enhanced with data provided by additional machine sensors. This is accomplished by the supplied OPC UA Integrator. Again the machine manufacturer is able to integrate his own machines in standardized infrastructures and at the same time differentiate himself from the competitors, e.g. with features such as a continuous state analysis by means of vibration and temperature data. Additionally, freely used data endpoints allow for integrating customer- and production-specific data such as order number, batch number etc. Furthermore, it is possible to load necessary process parameters into the CNC, e.g. part programs and tool parameters. Thus, an automated data supply is achieved which assures high process reliability.
Besides the solution described above, SIEB & MEYER also offers a server-oriented interface solution: The "SM IIoT Platform" is connected to various CNC controls and displays their data with all available features. This variant can also be used for retrofitting older machines (CNC 8x.00).
Technical properties of the solution:
- basics: self-describing data model organized in a tree structure
- modern microservice architecture
- data content according to JSON format
- intern broker architecture decouples data source (CNC) and data sink (OPC UA server)
- core component: Service Manager
- manages data model
- manages services such as
- 9x Connector (CNC 93.00, CNC 95.00)
- 8x Connector (CNC 82.00, CNC 84.00, CNC 82AS)
- OPC UA server
- further services: sensors, OPC HA
- intern services
OPC UA is the future standard data interface for SIEB & MEYER available on the current CNC 95.00 and CNC 93.00 systems, if required. Since February 2021, the interface can be used for the preceding CNC 8x.00 systems (software version 21.02.003), too. Hence, it is possible to fully integrate already existing systems. This allows for CNC controls to be easily used in future-oriented infrastructures. Thus, customers can flexibly address increasing demands of modern production environments.