Minimal Motor Heating with High-speed Converters by SIEB & MEYER
Technical papers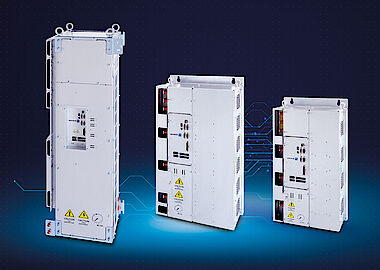
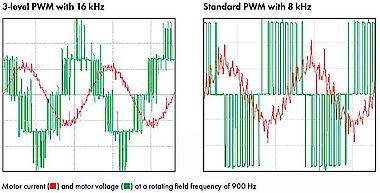
Cool performance in sustainable applications
Keeping the motor cool is essential for the operation of high-speed motors. These are not only the heart of machining centers and machine tools but also contribute to the energy transition when used in turbo compressors and flywheel energy storage units amongst others. The frequency converters of the SD4x product family by SIEB & MEYER minimize converter-based motor losses, which results in low motor heating and improved system efficiency. Beside saving energy and costs, users benefit from outstanding manufacturing quality.
About 90 % of the power losses caused by the converter occur in the rotor. These losses result in heat that can damage the motor. Due to the typically small rotor volume of high-speed motors, the temperature rise becomes even more problematic. This was precisely the challenge that SIEB & MEYER focused on when developing the SD4x product family. With a suitable control technology and a well thought-out topology, the high-speed converters of the Lueneburg-based high-speed experts enable motor currents with minimal harmonic frequency components. Compared to competitive products the losses are reduced by up to 90 %, which also reduces motor heating correspondingly. The low temperatures in turn extend the service life of the ball bearings typically used in machining spindles and also improve the manufacturing quality.
The objective: the perfect sine curve
How to generate a motor current with the desired high quality? "To answer this question, it is important to know that all currents that differ from the ideal sinusoidal shape produce losses in the motor," explained Torsten Blankenburg, CTO at SIEB & MEYER AG. "This part of the motor current is generated by the converter and is called ripple current. The ripple current overlays the sinusoidal motor current." The generated ripple current depends on the switching frequency, the DC voltage of the converter and, above all, the motor inductance. Low inductances cause considerable ripple currents. This is especially problematic with high-speed synchronous motors, as they have inherently small inductances. The resulting rotor heat can have an enormous impact on rotor stability, permanent magnets and bearings. Particularly at high rated motor speeds, these problems become apparent.
As a countermeasure, standard converters with two-level pulse width modulation (PWM) and low switching frequency are often used in combination with LC filters. These customized solutions are based on passive electronic components that allow either smoothing the switching edges of the output pulse pattern via dv/dt filter or even an approximation of sinusoidal motor voltages and currents. However, using LC filters comes with additional costs, increased space requirement, more weight as well as losses in efficiency. In addition, the prior dimensioning of the filter for the specific application requires time and flexibility.
The solution: three-level technology and higher switching frequencies
Another option is to increase the switching frequency for PWM. The rule of thumb here is that doubling the frequency will reduce the ripple current by half. There are technical and economical limits, though. On the one hand, high-frequency power transistors are more expensive for higher voltage ranges. On the other hand, the switching losses in the output stage increase drastically, which has a negative impact on the efficiency and the cooling effort. Apart from that, not all motors can cope well with increased switching frequencies. In some cases, especially with synchronous motors without segmented permanent magnets, increasing the frequency reduces the motor losses only marginally.
An alternative is the three-level technology as implemented, for example, in the SD4M by SIEB & MEYER. Compared to two-level technology, only half the voltage is supplied to the power semiconductors of the output stages. This makes the use of power semiconductors for lower voltages possible and these can switch faster. The result: there are fewer switching losses in the output stage and the switching frequency can be increased significantly. At the same time, the motor is loaded with only 50 % of the voltage jumps compared to two-level technology. Three-level technology can reduce the losses generated in the rotor by about 75 %. Combining three-level technology with a higher switching frequency reduces the rotor losses by up to 90 % and, in many cases, eliminates the need for LC filters.
More efficient climate-friendly applications
The effects on efficiency, CO2 emissions and costs when using a SIEB & MEYER frequency converter become clear with the practical example of a wastewater treatment plant ventilated by turbo compressors or turbo blowers.
This application is characterized by round-the-clock operation of the compressors or blowers; 365 days a year. Therefore, the plant efficiency is an important factor and keeping the motor heating as low as possible the big challenge. SIEB & MEYER meets these requirements with the SD4M and its multilevel output stage, which increases the efficiency of the turbo compressors or blowers by several percentage points.
Another application example for the SD4M series by SIEB & MEYER is a solution for fast charging stations in areas with a weak grid structure. The fast charging station works in combination with a flywheel energy storage unit that provides the energy required for charging the vehicle and stores energy between the charging processes.
The big challenge of this application is that the rotor of the flywheel works in a high vacuum. With the resulting high insulation effect, the heat can only dissipate as radiant heat. Moreover, this system uses magnetic bearings, i.e. without contact, so that the rotor heat cannot be transferred outward via the bearings. "That means, this system requires the lowest possible heating to work properly," summarized Torsten Blankenburg. "Our frequency converters generate minimal heat and can therefore optimally support such applications and even make them possible in the first place."
Optimized control of IPM motors
Another talent of the SD4x family is the optimized control of IPM motors. IPM motors make significantly higher demands on the frequency converter. For one, the current angle in dependence of the operating point must be optimally applied to the machine to achieve the maximum possible torque at each operating point. In addition, the frequency converter must consider the dependency of the motor inductance on the current and frequency to reach optimal efficiency. Using special control structures, the SD4x frequency converters can accurately determine the described dependencies and optimally control them at the respective operating point, which results in the optimal torque at the lowest possible motor current. This minimizes the losses in the motor and converter, improves the energy balance and reduces CO2 emissions.
SD4x: development platform for a future-proof device series
Already some time ago, SIEB & MEYER introduced the development platform SD4x. On this basis, the company now continuously develops a future-proof device series. The frequency converters support new interfaces and offer a number of additional functions. Users benefit from higher speeds and from a significantly enhanced performance. Thanks to an integrated position controller, SD4x converters can now execute highly precise positionings. The speed and current controller have remained unchanged compared to the well-established SD2x series.
"Our aim is to drive high-speed motors dynamically and with even less power losses," said Blankenburg. "Therefore, we now support PWM switching frequencies of 24 and 32 kHz." For an even finer modulation of the sine-wave signal, a commutation angle control for 32, 48 and 64 kHz is also integrated. The result is an almost optimal sine with nearly no harmonic currents. The power loss caused by the PWM can be reduced to a small fraction.
"Optimized performance, higher speeds as well as the lower motor heating without sine-wave filter – these are substantial advantages of the SD4x product family," summarized Blankenburg. "The enhancements allow optimizing the production quality for existing applications and, beyond that, exploring completely new fields of application."